How to Choose the Best Welding Rod for Different Metal Types
Welding, a process that involves joining metals by heating them until they melt and then allowing them to cool and fuse. It is a fundamental skill for beginners and professional welders. Understanding the various components of the welding process is crucial, and one of the most significant elements is the welding rod. This consumable plays a pivotal role in ensuring the quality of the weld, empowering you with the knowledge to create solid and stable joints.
In this article, we will explore what a welding rod is, its types, and how to choose the right one for your project. So, let's move on to the main topic:
What is a Welding Rod?
Welding rods, also known as electrodes, are welding materials that melt and flux during operations such as stick welding. To use a welding rod, you must first attach it to your welding equipment, creating an electric arc between the base metal and the welding rod. Because the electric arc is so intense, it quickly melts the metal, making it ready for welding.
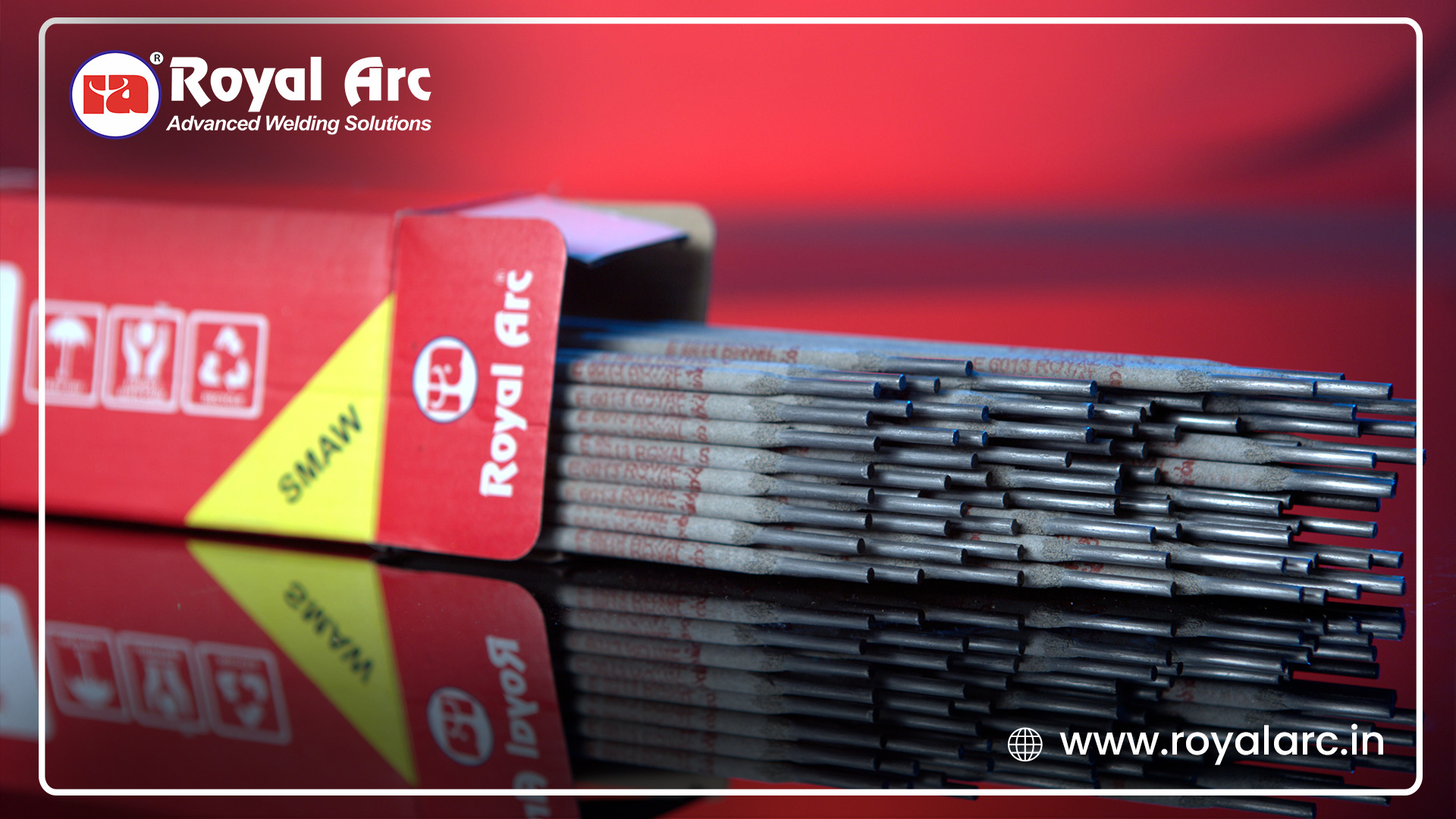
The base material, which is the part being joined, and the consumable, which is the material used to form the joints, are crucial in the welding process. Due to their shape, these materials, also known as base plates or tubes, flux-cored wire, consumable electrodes, etc., play a significant role in the welding process.
Why are welding rods necessary?
The right welding rod is not just a choice; it's a crucial decision to make or break your project. It's the key to achieving a strong, stable, high-quality weld. The type of welding rod used can affect various factors, such as the strength of the joint, the kind of metal being welded, and the appearance of the weld bead. For example, selecting a rod that matches the base metal is essential to avoid joint weaknesses or weld defects.
Types of Welding Rods
Several welding rods are available, each designed for specific techniques and metal types. Let’s take a look at some of the most commonly used welding rods in detail:
1. Mild Steel Welding Rods (E-6010, E-6011, E-6013)
Mild steel welding rods are one of the most commonly used welding rods. They are versatile and easy to handle. They are suitable for most general-purpose welding tasks. These rods work well for welding low-carbon steel and provide high deposition rates.
- E-6010 and E-6011: Known for deep penetration. These rods are perfect for welding rusted or painted surfaces.
- E-6013: These rods create a smooth and clean weld. They are easy to control. These are great rods for people new to welding.
2. Stainless Steel Welding Rods (E-308, E-309, E-316)
Stainless Steel Welding Rods These are designed to weld stainless steel and other corrosion-resistant materials. They provide excellent resistance to oxidation and work well in high-temperature environments.
- E308: This rod is widely used for welding austenitic stainless steel.
- E309: These are quite suitable rods for welding dissimilar metals.
- E316: Provides excellent resistance to chemical corrosion. Making it ideal for welding in aggressive environments.
3. Cast Iron Welding Rods
Cast iron rods are used to weld cast iron components. These are designed to prevent cracking, a common problem when welding due to the brittle nature of cast iron. Nickel-based rods are popular for cast iron applications because they produce strong, ductile welds.
4. Aluminum Welding Rods
Aluminium welding rods are used for welding aluminium and its alloys. They are softer than other rods and require special handling to avoid contamination. They are ideal for repairing aluminium parts or creating lightweight structures.
5. Special Welding Rods
Special welding rods include welding electrodes that are designed for specific applications. Hard-facing rods are used to apply welds to the surface of worn parts or in underwater welding. They are formulated to meet the unique requirements of particular welding environments.
Factors to consider when choosing a welding rod
Choosing the right welding electrode is crucial to the success of your project. Here are some points that can help you choose the right welding rod:
1. Base metal type
The welding rod you choose should match the metal you are welding. For example, stainless steel rods are suitable for stainless steel metals, while aluminium rods are required for aluminium projects.
2. Welding position
Some rods are designed for specific welding positions such as flat, horizontal, vertical or overhead. For example, E6010 and E7018 are versatile and suitable for various situations.
3. Joint design
The type of joint and its accessibility also play a role in choosing the right rod. A thinner rod may be required if the joint is narrow or inaccessible.
4. Welding current
Some rods are compatible with AC (alternating current), DC (direct current) or both. It is essential to ensure that the welding electrodes match the capabilities of your machine.
5. Desired weld characteristics
Consider what you want the final weld to look like. Some rods create a smooth, shiny weld bead, while others create a rough finish. If aesthetics are important, choose a rod that provides the desired look.
Conclusion
Understanding welding rods and their applications is essential to produce high-quality welds. We read above how important it is to choose the right welding rod for your project. At the same time, selecting electrodes from the right company is most important for the success of your project. Quality welding rods from Royal Arc will be effective for all your projects.