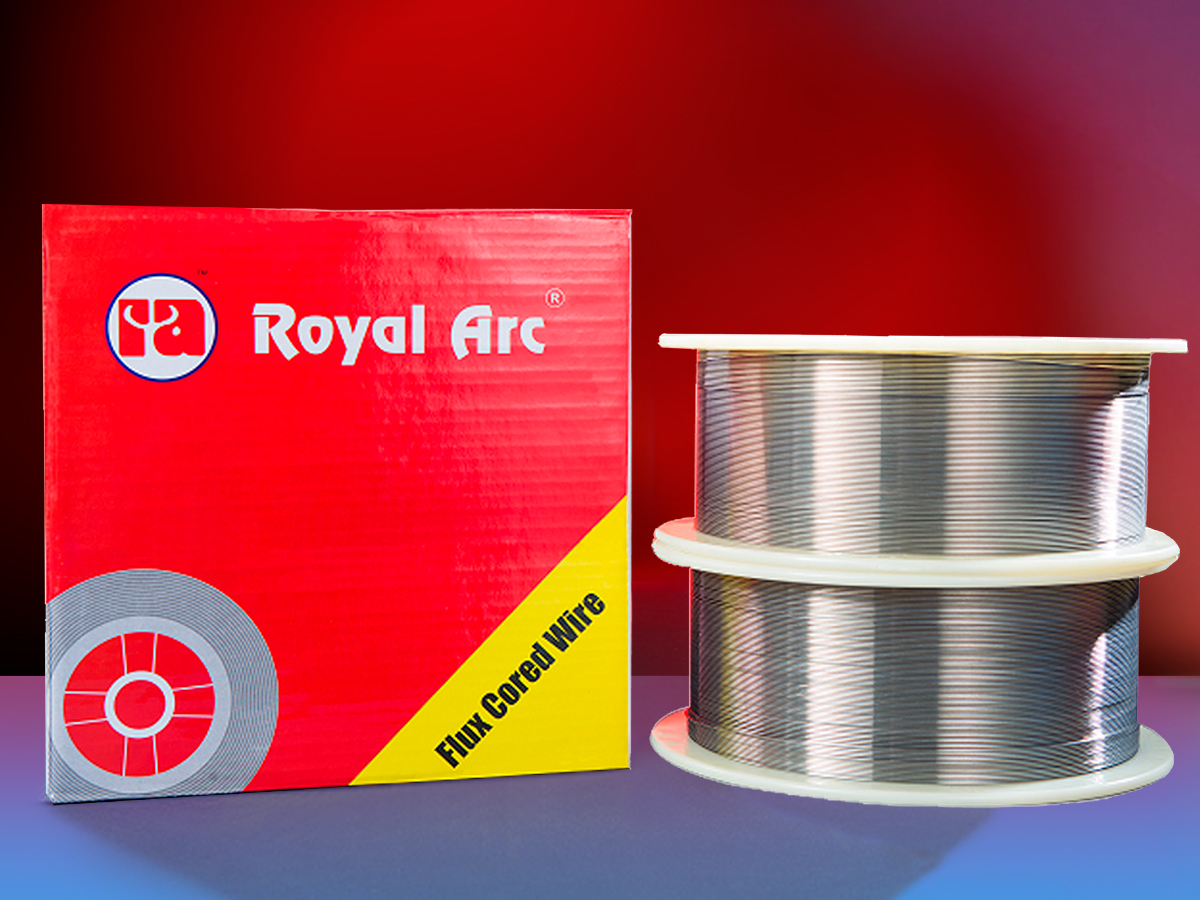
Flux cored Wire Performance Optimization: Tips to Increase Productivity
Are you looking to increase the productivity of your flux-cored wire operations? Flux cored wire can be a great way to improve the efficiency of your welding process, but it's important to optimise its performance to get the most out of it.
Flux cored wires are a great option for welding because they provide high deposition rates, good weldability, and low fumes. However, there are a few things you should know before using them. This blog post will cover everything you need about flux-cored wires to make the best decision for your next welding project.
They offer high deposition rates and good weldability. Additionally, they produce fewer fumes than other welding methods, which is important for your health and the environment.
Why is flux-cored wire performance very important?
There are a few key factors that make this type of wire so important:
It provides superior arc stability and low spatter levels compared to other types of wires. It is due to the way the flux core helps shield the arc from oxygen and other atmospheric gases.
Flux cored wire produces less slag than solid wire, which means it requires less time for cleanup after welding.
People can use it with AC and DC power sources, giving welders more flexibility when working on projects.
If you're looking for a high-quality welding wire that will provide superior performance, flux cored wire is the way to go. Keep these factors in mind when deciding, and you'll be sure to find the right wire for your needs.
Flux cored wire provides many benefits for those who frequently weld. The superior arc stability and low spatter levels are just two of the reasons why this type of wire is so important.
Factors that contribute flux cored wire performance
Flux cored wire provides many benefits over traditional solid wire electrodes, including higher deposition rates, improved operator control, and easier out-of-position welding. Flux cored wire can provide excellent weld quality and productivity with proper equipment and techniques. In addition, optimising flux cored wire performance can result in significant cost savings.
Several factors can impact the performance of flux cored wire. The type of metal, the welding process used, the amperage and voltage settings, and the travel speed are just a few variables that can affect weld quality and deposition rates. By understanding how these factors influence weld quality and productivity, operators can make adjustments to optimise performance.
More deposition rates are generally possible with flux cored wire than solid wire electrodes. It is due to the higher current density used with flux cored wire. In addition, the operator has more control over the welding process when using flux cored wire. It allows for better weld bead placement and improved out-of-position welding.
The main factors that affect the performance of a flux cored wire are the chemical composition of the wire and the gas used for shielding.
The chemical composition of the wire determines how well it will flow and how strong the arc will be. The gas used for shielding protects the weld from contamination by oxygen and other gases.
Many types of flux cored wires are available, each with its characteristics. The type of wire you use will depend on your welding application. For example, wires are designed for thin welding metal sheets, while others are better suited for thicker materials.
Gas shielded wires usually produce less spatter and have a smoother arc than self-shielded wires. They also tend to be more expensive.
Self-shielded wires are easier to use because they don't require a gas tank and hose. They are less expensive. However, they produce spatter and have a rougher arc. Flux cored wires are easy to use and provide good welds.
Here are a few tips to help you do perfect optimisation
- Use the right gas mix: The gas mix used for flux-cored welding is important, as it can affect the arc's stability and the weld's quality. Consult the flux cored wire manufacturer to find the right mix for your specific wire.
- Adjust your travel speed: The speed you travel along the weld joint can also impact productivity. If you're Welding too slowly, you'll increase the amount of time it takes to complete a weld, while welding too quickly can cause problems with bead appearance and overall quality. Try different speeds and see what works best for you.
- Maintain proper tension on the wire: It's important to maintain proper tension while welding, as this can help prevent other feeding problems.
By following these tips, you can optimise the performance of your flux cored wire and improve your welding productivity.