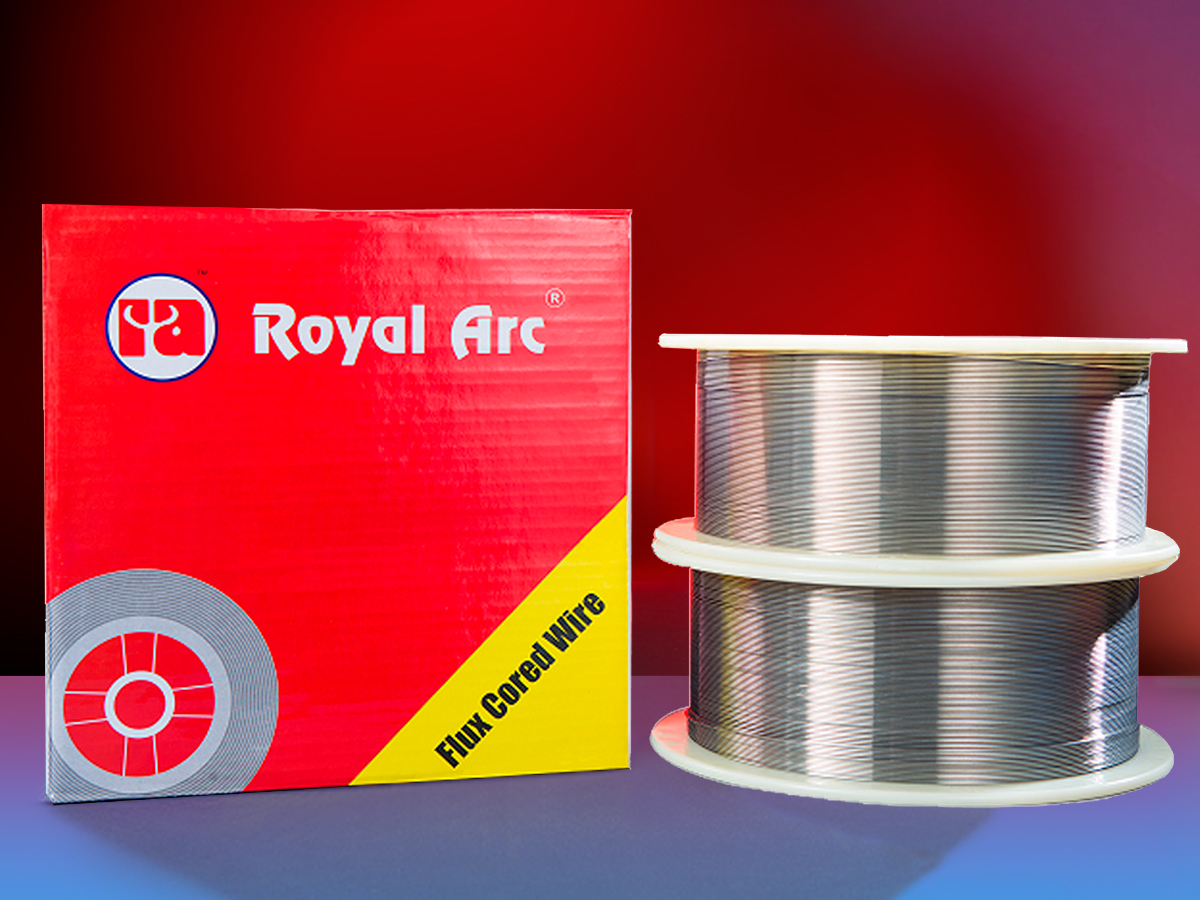
How is Flux-cored arc welding different from MIG welding?
Mig welding is a type of arc welding used for metals, non-ferrous metals, and ferrous metals. Flux-cored arc welding is a type of arc welding that uses a flux-cored wire electrode instead of an inert gas shield to protect the weld pool. Flux cored wire manufacturers offer different types of welding consumables. Let’s explore more arc welding and MIG welding.
What Is MIG Welding and How Does It Work?
Mig welding is an arc welding that uses a wire feeder to create the arc. It's also known as "MIG" for short. MIG welding is an arc welding process that uses a wire feeder to create the arc. It's also known as "MIG" for short. There are two major types of MIG welders: stick and gun welder. The main difference between them is their design and how they work, but both work by using an electric current to heat metal to create the weld joint.
Does MIG Welding Have the Same Advantages as Flux Cored wires?
MIG welding was an easier alternative for flux cored wires and arc welding in the past. However, it’s evident that MIG welding has its advantages and disadvantages.
The advantages of MIG welding are that it is faster, less expensive, and more reliable than a flux-cored arc. It also requires less skill to use it. The disadvantages are that it is easier to make mistakes with the process, and there is a chance of damaging surrounding areas when using MIG welding equipment.
Advantages of Using a Flux Core Arc Welding
Flux-cored arc welding has several advantages over MIG welding. It is not only easier to use, but it also provides better weld quality and faster production rates.
Flux-cored arc welding is a type of welding that uses a wire electrode instead of a consumable metal electrode. It is commonly used in industrial settings because it can be used with many different types of metals, and the wire electrodes are reusable. Flux cored wires and arc welding is a new type of welding used for different purposes. It has been gaining popularity with the advent of new technologies because of its versatility.
The advantages of using Flux-cored arc welding over MIG welding are:
-Welds are stronger than those made with MIG welding.
- Faster production rates because the molten metal does not have to cool down between each weld.
- Less likely to cause puddles, which leads to fewer defects on the welded surfaces and less downtime for repair work.
- It is more cost-effective than MIG welding.
- It produces less heat, which makes it safer.
- The process requires less equipment and training.
- There are no fumes generated through the process.
Is flux-cored arc welding better than MIG welding?
MIG welding is a versatile and popular process for joining metals. It is also known as metal inert gas welding because it uses an inert gas, typically argon or helium, to protect the weld from oxidation. Flux-cored arc welding has been around for a long time, but its popularity has been dwindling in recent years.
MIG uses an electric current to create a melting point between two pieces of metal, while flux-cored arc welding requires a high-temperature flame to melt the metal and fuse them.
MIG is one of the most popular processes in the industry today, especially in manufacturing. Professionals who need to weld thin materials like aluminium or copper use this.
Are you looking for reliable flux cored wire manufacturers?
Get in touch with us!