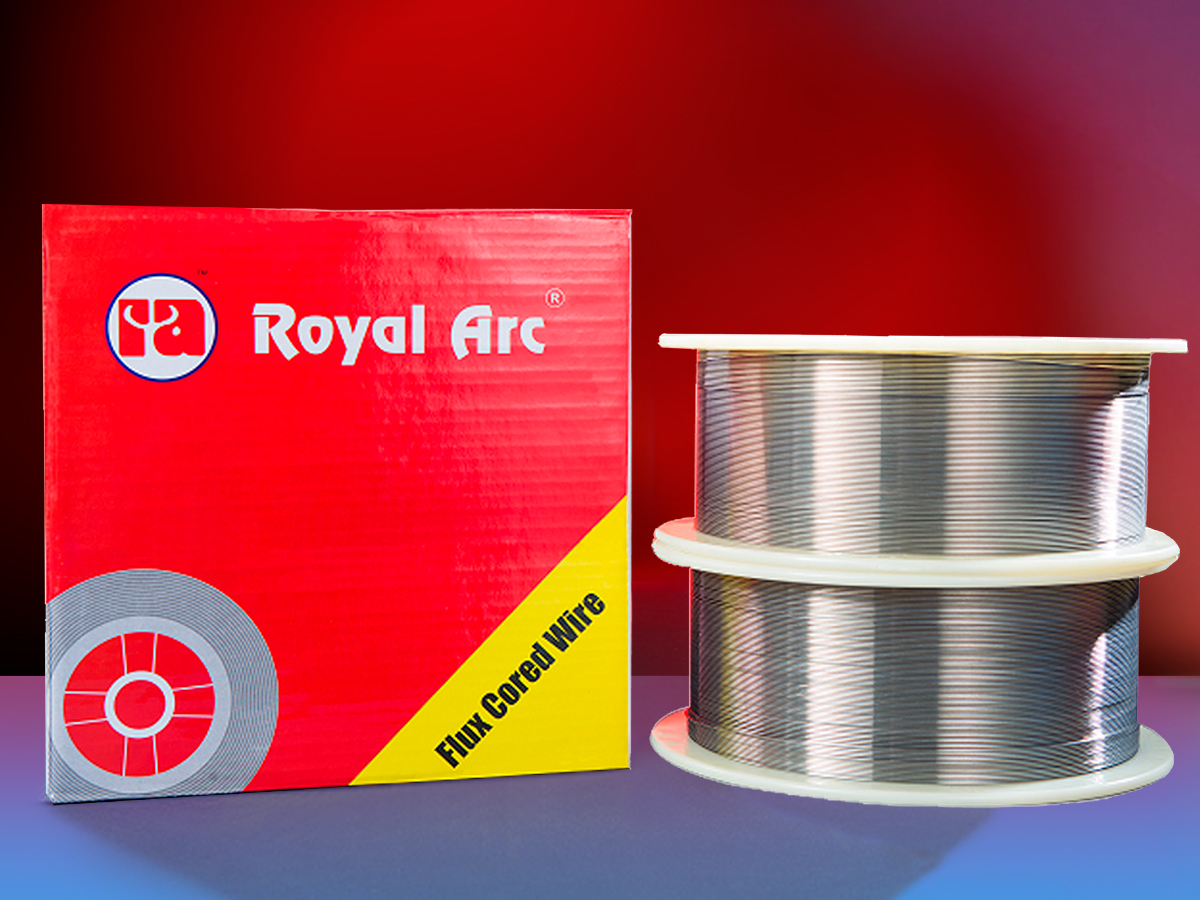
The Advantages of Flux Cored Wire for MIG Welding
Flux-cored arc welding (FCAW) is a type of arc welding that uses a consumable electrode called flux cored wire to create the weld. The process uses an electric arc to heat metal electrodes and melt the weld pool. A high-frequency current supplied by a power source creates the arc
The flux cored wires involve solid or hollow metal and contain a chemical compound called flux which helps shield the weld pool from atmospheric contamination.
Flux-cored arc welding is an excellent choice for certain types of welds, such as those that are difficult to make with other methods like gas tungsten arc welding or shielded metal arc welding. This type of welding is also suitable for dirty work environments where dirt and debris can interfere with other types of welding processes.
The role of flux-cored in arc welding:
The welding process utilizes the flux-cored wires as a type of filler material. It comes from a metal powder and flux, which requires compression into a solid metal rod.
The role of flux cored wires in welding is to provide welds with a metal filler that doesn't require consumption during the welding process. This way, you can use it to fill gaps between two pieces of metal without worrying about running out of filler material.
Flux-cored electrodes help in creating deep welds with less spatter and slag. They are also more efficient than solid wires because they can be fed continuously into the weld pool. Also, they do not need to be cut at different points during the process. The flux cored wires are made from the metal alloys that give greater arc stability.
Why Should You Use Flux Cored wires for MIG Welding?
The flux-cored wire is a type of welding wire used in the MIG welding process. It is a handy tool for anyone who wants to do this type of welding. The flux-cored wire contains an inert gas and a fluxing agent, which, when combined with an electric arc, creates strong welds that have a good appearance. Flux-cored wires are highly useful in both steel and aluminium applications.
MIG welding is one of the most popular methods for joining metal parts together. The process uses a consumable electrode called flux-cored wire (FCW) to create welds with good appearance and strength. It uses an inert gas, such as argon, because it does not react with the welding flux. This provides a safe environment for the weld pool to develop. The flux contains iron and other metal oxides that form a protective coating on the workpiece. It helps to prevent oxidation of the metal joining surfaces. An electric arc oxidizes the iron in the flux. As a result, it creates a molten slag that is removed from the joint. Flux-cored wires are available in a variety of gauges and lengths. The thickness of the flux layer also affects welding quality and electrode lifespan.
The flux-cored wire is termed as "self-shielding" wire because it has an outer flux coating.
Flux cored wires are available in many different diameters and thicknesses. The most common size for general purpose use is 0.035 inches. It is also the most popular size for automotive applications.
Flux cored wire manufacturers suggest that flux-cored wires cannot be used with gas-shielded processes like TIG or plasma cutting because they don't have an outer layer of shielding gas and are not suitable for use in the GMAW process either.
Why Would You Want to Switch to Flux Cored Wire?
Flux-cored wire has been around for a while but is experiencing a resurgence in popularity. Manufacturers are taking notice and are now producing the wire in several varieties to suit the needs of different industries.
Flux cored wire manufacturers offer a type of metal filler metal used to weld ferrous alloys together. It has an inert gas sealed inside the welding wire which provides shielding from oxygen, prevents oxidation and allows for more efficient welding.
This type of filler metal can be used in many industries, such as automotive manufacturing, shipbuilding, construction and more because it helps weld steel together without using fluxing agents or shielding gases.
Are you looking for a reliable flux cored wire manufacturer?
Get in touch with us!