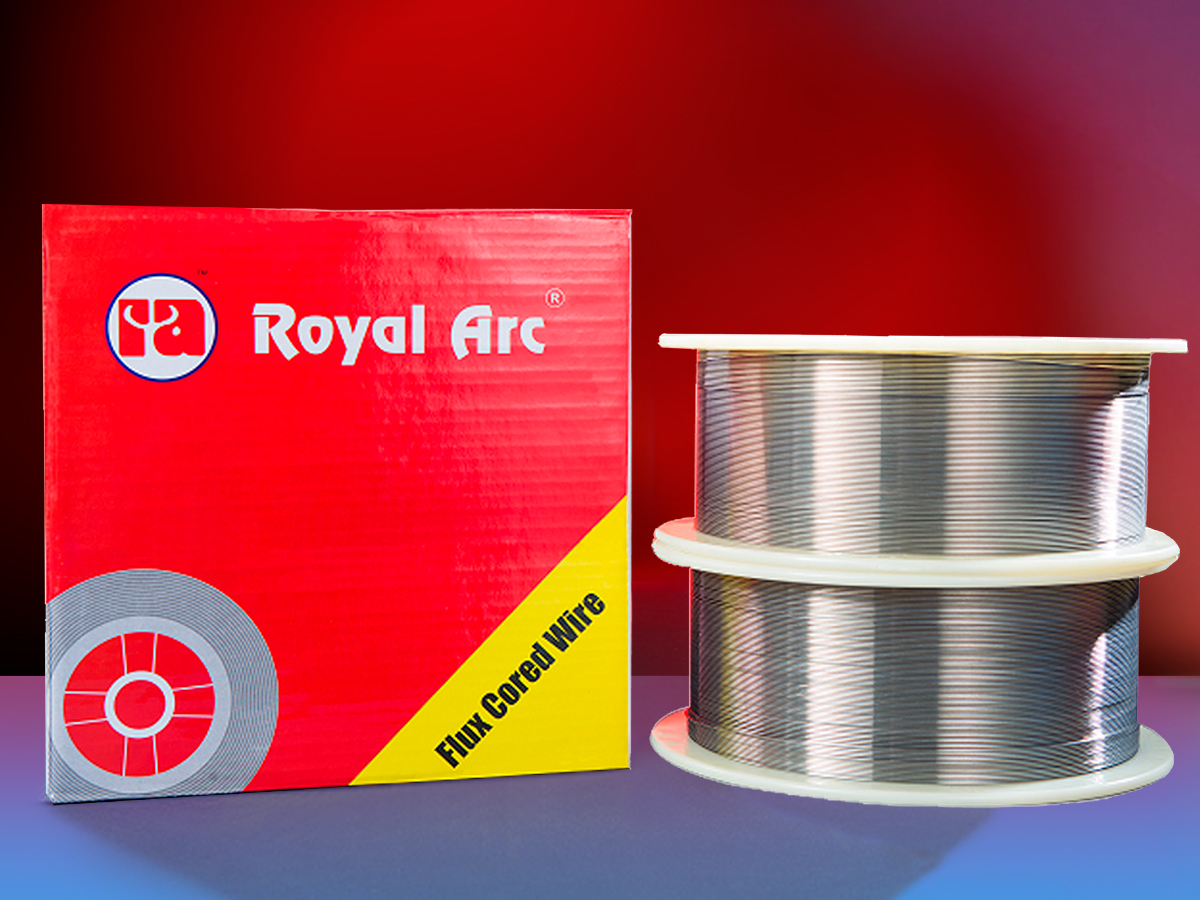
The Complete Guide to Self-shielded flux-cored Wires and Gas-shielded flux-cored Wires
Self-shielded flux cored wires are a type of metal-cored wire typically used in welding. It has a shielding gas which protects the weld pool from contamination. The shielding gas is inert and does not react with the weld metal.
Gas-shielded Flux cored wires are a type of metal-cored wire typically used in welding. It does not have any shielding gas, so it may be more reactive to the weld metal.
Fluxes are materials that help clean and protect metals during welding. Flux-cored welding starts by clamping the parts together and running an electric current through them. The heat from the weld melts the base metal, and then a flux coating is applied to it. The molten metal creates a slag when it cools, which is then removed with a wire brush or skimmed off with a tool.
Self-Shielded Flux Cored Wires vs Gas Shielded Flux Cored Wires
Self-Shielded Flux cored Wires are popular among welders because they offer a lower cost than gas-shielded wires. They also have a higher tensile strength and can be used in all positions. Gas Shielded Flux Cored wires are more expensive than self-shielded wires, but they offer better environmental protection. This type of wire is supportive in underwater welding jobs, where the environment is moist and humid. The materials that make up flux-cored wire include copper, nickel, and tin.
The metal used within the wire forms a flux when exposed to a certain form of energy. This is what creates the arc that makes welding possible. The flux also allows the metal to weld to other metals without melting or burning them. Copper and nickel are often the first metals used for flux-cored wires. Flux cored wire manufacturers offer much higher quality than tin. When using tin, flux-cored wires are often known as tungsten-in-tube or reactive wires. One advantage of flux-cored wires is that they can be welded with a gasless process without the need for gas because the flux is the shielding agent. One disadvantage is that the flux may not be as effective as other types of wire when heated.
What to Consider When Selecting the Right Flux Cored Wire
When selecting the right type of flux-cored wire, there are many things to consider. The type of material you will be welding, the thickness, and the voltage are all factors. Flux core welding is a process that uses an electric arc to heat and weld metal together. This process is beneficial for welding thin metals that require high penetration and uniformity. The wire created from this process is called flux-cored wire.
There are two basic types of flux cored wire: soft and hard.
Soft cored wire is softer, has a better arc, and has less heat than hard cored wire, but it also reduces the weld metal's strength by 20%.
Hard cores can withstand higher temperatures but may require a thicker metal to be welded, thus reducing the penetration level of a weld.
Thickness:
It is the thickness of the metal that you want to weld. The size and shape of your wire will depend on what size and shape of material you are welding. For instance, if you are welding a large flat piece, it would require a much bigger wire than if you were welding something round.
Voltage:
It is how much electricity is being put through the wire. A higher voltage will produce a hotter and more powerful arc, but can also lead to excessive heating and fire. A lower voltage will produce a weaker arc but with less risk of fire.
Speed:
It is how fast the electric current runs through the wire. An increase in speed will increase heat and power levels, but with increased speed also comes more time for the wire to cool before it can be used on another piece of metal.
Power consumption:
Current refers to the amount of electrical charge flowing through an electric circuit. It is about the consumption of electricity. The current rating indicates the requirement of the number of amps per hour.
Amperage:
It measures the amount of electricity put through a circuit or what size wire can be run through the circuit. Amperage measurement is in amps, where 1 amp generates a potential difference of 1 volt.
Frequency:
It is how many times per second the electric current runs through the circuit. A higher frequency will generate more heat and increase electrical interference with other devices in your shop or home.
Are Self-Shielded Flux-Cored Wire Better Than Gas Shielded?
A self-shielded flux-cored wire is better than a gas-shielded wire because it doesn't require shielding gas for the process. This means that there is no limitation by the location of a gas tank and can use a self-shielded flux-cored wire anywhere. Gas shielded wire must be used in an environment with a constant flow of shielding gas, usually supplied by a tank. The location of this tank can limit where and when welding can occur. A self-shielded flux-cored wire is better for welding in wet environments because it does not require a shielding gas. This means that the welders can work in wet environments without worrying about waiting to refill the gas tank and for the shield gas to be re-supplied. The electric arc needs less shielding gases than a natural gas arc.
Are you looking for reliable flux cored wire manufacturers?
Get in touch with us!