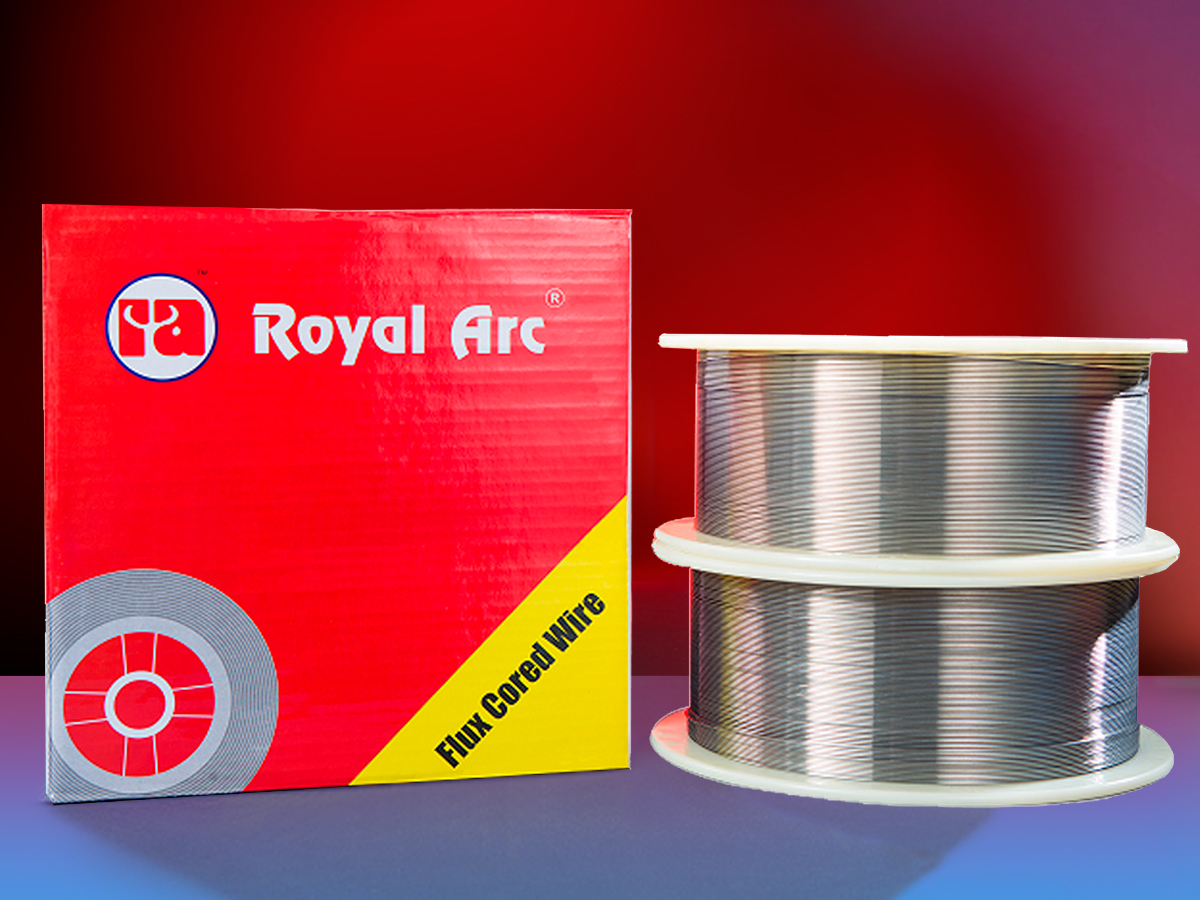
The Difference Between MIG and TIG Welding Wires and When to Use Each One
Beginners need to know about MIG and TIG wire, which are two different welding processes that provide different benefits during the welding process. Understanding the differences between MIG and TIG welding wires can enhance your skills.
In this blog post, we will explore how MIG wire and TIG wire differ and provide guidance on when to use each to maximise efficiency while achieving high-quality welds.
The two types of welding wires
MIG and TIG welding wires are very popular in the welding process. They are often referred to as filler materials, as they fuse different pieces of metal with precision and strength. Both types of wires have advantages and disadvantages depending on the task at hand; for example, MIG wire is more malleable and can handle thicker material with less heat build-up, versus the more brittle TIG wire which requires higher temperatures and is better suited for tighter welds on thinner sheets of metal. Either way, both wires offer a high-quality, durable finish for many applications. MIG and TIG wires differ in how they produce a weld, work materials, and other factors. Here are more details about these two welding wires:
MIG Welding Wire: - stronger welds, faster process, and less expensive materials
MIG welding stands for metal inert gas welding. This process involves feeding of a spool of wire electrodes through a MIG gun to a weld. MIG welding uses a shielding gas to protect the weld and the arc from atmospheric contamination. The gas typically used in MIG welding is a mix of Argon and Carbon Dioxide, sometimes Argon and Oxygen, Argon and Helium, or Argon and Hydrogen. MIG wire is an incredibly efficient way to create strong welds quickly and economically. Not only is it exceedingly fast compared to traditional welding, but the welds it creates are incredibly strong. It also allows users to use various materials, including cheaper alloys, by maintaining a lower temperature while welding than other processes. This reduces costs in purchasing materials and time associated with the process. The ability to do short arc welds makes MIG welding perfect for thin-walled steel or aluminium. The combination of speed, strength, flexibility, and affordability makes MIG wire one of the most popular welding methods today. .
TIG Welding Wire: - greater control over your welds, more accurate results, and greater heat transfer
TIG wire in welding produces fine, precise welds. It uses a tungsten rod, and the filler metal is applied with a separate wire that the welder feeds into the weld pool manually. The lack of spatter or smoke makes it clean and perfect for thin sheets, small diameters, and difficult projects such as high-pressure vessels or structural engineering applications. A shielding gas, usually a mix of Argon and Helium, safeguards the weld from contamination. TIG welding offers numerous advantages to experienced and novice welders alike. By allowing greater control over the welds and offering a more precise result, this type of welding can save significant time and effort. Greater heat transfer is also an advantage of TIG welding, providing a more robust weld that can better withstand temperature extremes. Another advantage of TIG welding is that it offers more versatility than traditional arc welding, allowing users to work with different materials such as aluminium, stainless steel and copper without worrying about external gases or fluxes. It's no wonder that TIG welding has become the go-to choice for precision welding jobs worldwide.
When to Use MIG or TIG Welding:
When choosing between MIG TIG wire depends on the welded material. MIG welding is ideal for thicker materials, especially heavy-duty projects like stainless steel and aluminium. It can also build heavy weld layers in small areas, such as welding machinery, automotive parts, or building framework. TIG welding is ideal for delicate materials such as thin metal sheets or non-ferrous metals like copper, bronze, brass, or titanium. It is perfect for creating precise, thin welds or finishes, such as with sculptures or ornamental metalwork. It is also used in welding bike frames or aircraft parts, where lightweight and strength are important. Additionally, TIG wire can produce beautiful welds; it is an art that takes time to master.
Conclusion: MIG TIG wires are different welding wires used for welding different materials. MIG welding is ideal for thicker materials, while TIG welding is perfect for delicate materials needing maximum control. The decision between MIG and TIG welding wires depends on the project’s requirements and the type of materials being welded. Understanding the differences will improve your welding quality.