Welding Electrode Types And Their Uses
Welding electrodes, a cornerstone of the welding industry, play a pivotal role in joining metals and providing strength. Their correct identification and selection can significantly influence the quality of your welding project, underscoring their importance in your work.
There are many leading welding electrode manufacturers in India, who produce high-quality electrodes. In this blog, we will discuss in detail the types of the best welding electrodes and their uses. So let's move on to today's main topic:
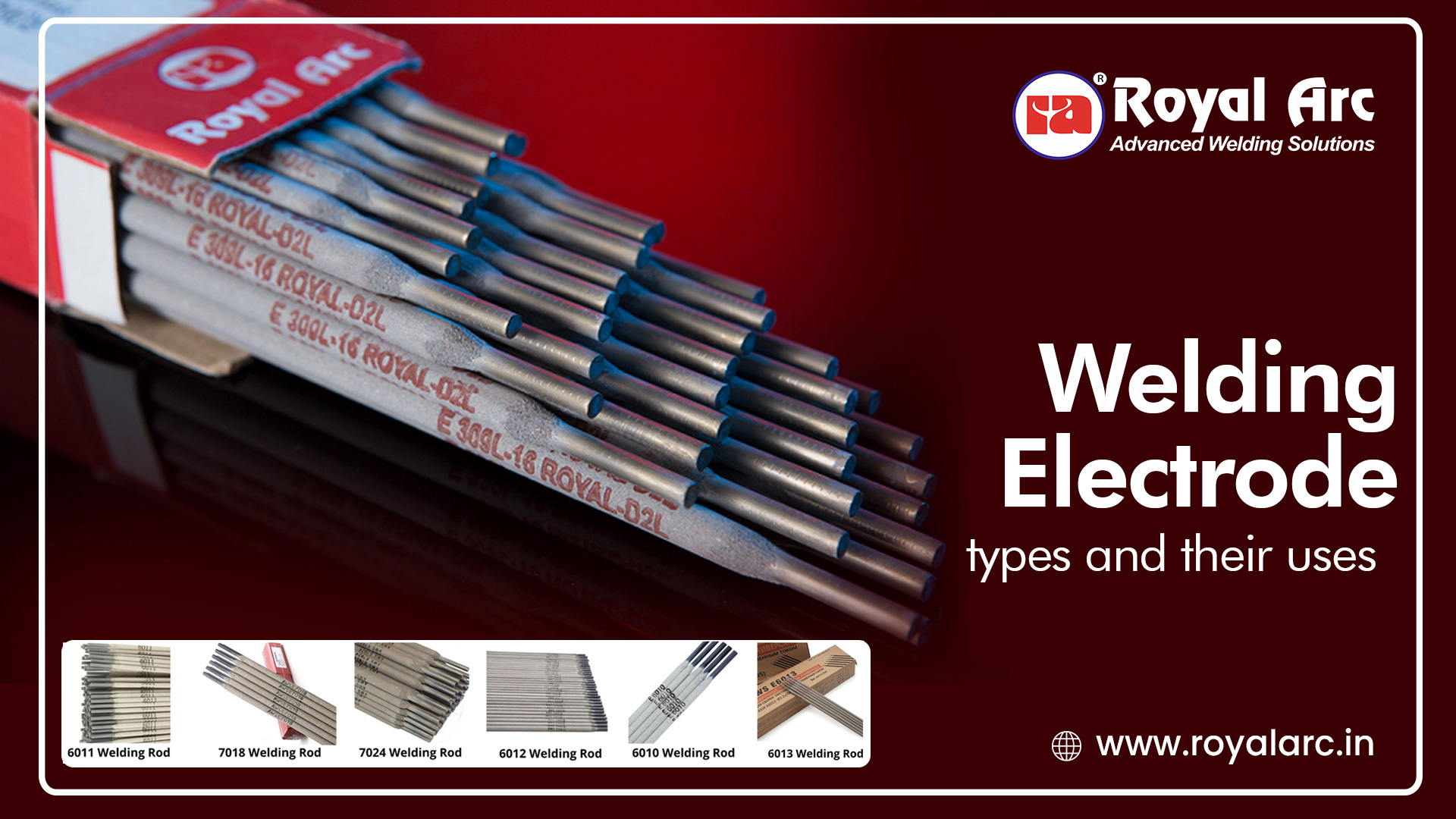
What is a Welding Electrode?
A welding electrode is a metal rod through which an electric arc is generated. It helps melt and join the metal surfaces. This gives a strong weld to your project.
Welding Electrodes are Mainly of 2 Types:
1. Consumable Electrode
These electrodes melt during welding and become a part of the weld. These are mainly used in SMAW, MIG, and SAW processes.
2. Non-Consumable Electrode
These electrodes do not melt independently but are welded through a filler metal. They are majorly used in TIG welding.
Types of Welding Electrodes and Their Uses
1. Mild Steel Electrodes
Mild steel electrodes are the most commonly used welding electrodes. These are made of low carbon steel and are used in general construction works, pipeline installation, and the automobile industry. The main reason for their popularity is their low cost and easy availability. These electrodes give a stable arc and deep penetration to your project during welding.
2. Low Hydrogen-Type Electrodes
Low hydrogen electrodes are best for applications with a high chance of cracking during welding. These electrodes keep the amount of hydrogen in the welding joint low, which maintains long-term strength in your project. You can use them in pressure vessels, bridge construction and pipe welding. Let me tell you that the quality and durability of the weld is extremely important here.
3. Low Alloy High Tensile Electrodes
These electrodes are commonly used for welding high tensile metals. These electrodes are widely used in heavy structures, machinery, railway engines and shipbuilding.
4. Stainless Steel Electrodes
Stainless steel electrodes are corrosion-resistant and perform well in high-temperature applications. These are commonly used in food processing, petrochemical, pharmaceutical and medical equipment manufacturing. Let me tell you that these electrodes produce corrosion-resistant welds during welding and are helpful in joining stainless steel surfaces.
5. Hard-Facing Electrodes
Their main purpose is to harden the metal surface of your project and increase its lifespan. You can use Hard-Facing Electrodes for surfaces that have to withstand extreme friction and wear. These are used for welding in industrial machinery, mining equipment, agricultural equipment and heavy construction equipment.
6. Casting Electrodes
Casting electrodes are specially designed to repair and weld cast iron. These electrodes are used in engine blocks, pumps, industrial machinery and casting manufacturing. You can use them when cast iron surfaces need to be joined or repaired.
7. Cutting & Gouging Electrodes
These electrodes are used to cut metal and prepare smooth surfaces. These are especially important in applications where metal needs to be cut and shaped quickly. You can use these electrodes in industries like shipbreaking, automobile repair and metal fabrication.
8. Low Heat Input Electrodes
You can use these electrodes in welding applications where excessive heat can damage the metal. These electrodes are specially made for welding thin metals. You can use low heat input electrodes mainly for electronics, jewelry manufacturing, and complex welding tasks.
9. Non-Ferrous Electrodes
The primary purpose of non-ferrous electrodes is to make welding of lightweight and corrosion-resistant metals easier. You can use these electrodes to weld aluminum, copper, brass, and other non-ferrous metals. These electrodes play a vital role in the aerospace, automobile, electrical appliances and communication industries.
How Do You Choose the Right Welding Electrode?
As we have seen, the success of your welding project hinges on the electrode you select. Your expertise and knowledge in this field are crucial in making the right choice. Let's delve into the key considerations when choosing the right welding electrode:
Type of base metal
Before welding, it is important to confirm that the welding electrode you choose is compatible with the base metal. Selecting the correct electrode according to the base metal type improves the weld's strength & quality. For example, E7018 & E6013 are used for mild steel.
Welding position
You may be required to work in different positions as per the need during welding. For instance, you might need to weld in a vertical, flat, or overhead position. It's important to remember that different types of welding electrodes are suitable for each position. Your attention to these details will improve the quality of the weld & reduce your positional challenges.
Environmental conditions
Your welding environment plays a vital role in electrode selection. Outdoor conditions, such as dirt & moisture, can impact the welding process. In such cases, E6011 welding electrodes, which perform well in these conditions, are recommended. High-quality low-hydrogen electrodes are ideal for indoor use for a clean and controlled environment.
Conclusion
Welding electrodes, a crucial part of the welding process, are designed for a wide range of applications across various industries. Their correct selection can significantly influence the quality and durability of the welding, making your construction work more safe and sustainable. The best Welding Electrode manufacturers in India, such as Royal Arc, offer high-quality electrodes that meet the diverse requirements of these industries, showcasing the versatility and applicability of your welding skills.