Strip cladding methods and benefits

The typical low alloyed economical base metal serves primarily as a load bearer. Cladding is a common welding technique that involves depositing material with required qualities on the base material’s surface. As a result, surface qualities like wear resistance, corrosion resistance, and much more are imparted to the substrate by the deposited sophisticated material. Surface techniques are becoming increasingly relevant to pressure vessel manufacturers. Hence, for manufacturing purposes it requires clad materials to grow to the point. Electroslag strip cladding and Submerged arc, among all welding methods, offer the highest deposition rate, enhanced bead properties, and seamless operation with essential welding equipment. A wide variety of materials makes use of the strip cladding as it is a versatile procedure. Because it is commonly used to clad finish formed components, it avoids the issues from hot or cold forming. Several submerged-arc welding process with strip modifications is highly valuable in increasing surfacing capacity. Now let’s see the process and benefits of each strip cladding method. Strip Cladding Process(Submerged Arc) Principle and benefits: There is no significant difference between wire-based submerged arc welding or strip cladding. Strip cladding can be done with standard submerged arc materials, in which the wire replaces a strip. The adjustable feed rollers and contact shoes on the welding head accept strips rather than wire. An electrical arc between the base material and welding strip is formed under mineral flux protection to provide the desired energy to melt the strip and the base material. Flux applies on dual sides of the strip. The base metal and strip are constantly molten under a layer of molten flux during the operation. After solidification, a thin slag layer covers the metal that deposits. The following are the key benefits of the strip process versus wire processes: A consistent penetration Limited penetration and low levels of dilution allows for a reduction in the number of layers required to achieve the desired qualities. The deposit quality is high and consistent; the beads’ distinctive solidification pattern ensures a very homogenous distribution of alloying components in the metal(deposited). Due to the lack of core solidification lines, classic hot cracking materials have very low sensitivity. • Highly flat surface with only a few bead overlays• Switching from wire to strip has a minimum initial investment cost.• High level of repeatability• High rates of deposition Electroslag Strip Cladding Process: Principle and benefits: The strip surfacing technique of electro slag strip cladding is a more recent discovery. People continuously feed a strip electrode into a shallow layer of molten electroconductive slag, which is essential. The Joule effect, caused by the welding current flowing through the liquid electroconductive slag, generates the heat required to melt the strip, the slag-forming flux, and the base metal’s surface layer. The electro slag strip method begins similarly to a submerged arc cladding process, with the process stabilising into the electro slag mode nearly instantly. The following are common characteristics of the process: The front side of the strip takes the flux A visible weld pool on the backside of the strip Only visible and infrared radiation, no ultraviolet radiation due to the lack of an arc An extra feature (magnetic control device) is applied to optimize the weld bead profile. Primary benefits of the process (Electroslag Strip Cladding) The electroslag approach gives substantially better deposition rates than the submerged arc strip cladding method, at the same amount of heat inputs and bead thickness, as the submerged arc strip cladding technique. It is essential to maintain the dilution with the metal to a minimum and typical dilution rates are somewhere between 8 and 10%. The process can obtain the requisite chemical analysis with fewer layers (e.g. low carbon stainless steel in one layer). ESSC is a very consistent and reliable welding process with a very minimal possibility of faults such as lack of penetration, slag inclusions,etc. Best practices for Optimum Production: To get the appropriate weld metal composition, you need to use the right strip electrode, flux, and welding conditions. Electroslag Strip Cladding requires a special ESSC flux with high electrical conductivity at high temperatures, and this usually occurs with a fluoride-rich flux. Determine the ideal voltage for ESSC by the flux and have a smaller voltage window than SASC. As a result, a high voltage causes spatter and unstable fusion, while a low voltage increases the possibility of short-circuiting due to the strip adhering to the base metal. The size and shape of the components to be surfaced dictates the desired strip width . Typical strip electrodes are 0. 5 mm thick 30-60-90 mm wide. The strong current creates a magnetic field that pulls the molten metal inward. Magnetic steering can help control this impact. When using electro slag strip cladding, apply magnetic steering when the strip width exceeds 60 mm. Choosing ESSC-specific equipment, accessories, and consumables can help manufacturers succeed. Consider Return on investment: Electroslag Strip Cladding may require more equipment than SASC, which may deter some enterprises from considering it. Therefore, cladding is often a high-amperage, high-duty cycle process. For some processes, the higher productivity and efficiency from increased travel speeds and deposition rates, lower dilution rates, and less welding consumables means a return on investment of only a few weeks. In addition, knowing which applications are most suited for the ESSC process can maximise the advantages and reduce costs. An alternative that increases productivity: Electroslag Strip Cladding can quadruple travel speed, boost deposition rates, and reduce dilution rates in automated processes. These productivity and efficiency benefits of Electroslag Strip Cladding can help firms save time and money while increasing competitiveness and profitability.
Welding Wire manufacturer | Royal arc
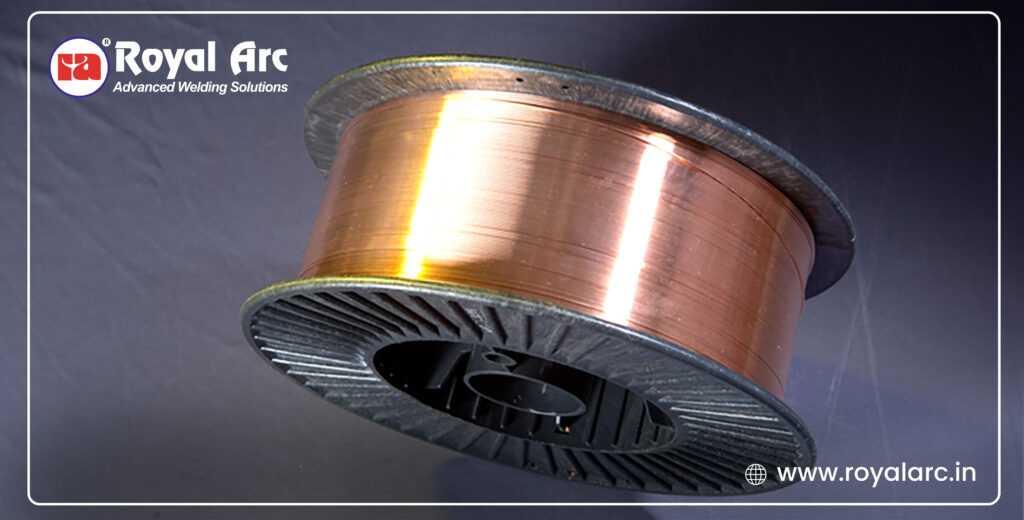
Ultimate Guide To Choosing The Perfect Welding Wire For Any Project When it comes to welding, choosing the perfect welding wire is crucial for the success of any project. If you’re new to the field or want to know more about Mig wire and Tig wire, this article is for you. In this guide, you’ll learn about welding wire essentials, including Mig wire and Tig wire, and also about choosing The Perfect Welding Wire For Any Project. So, let’s learn more about the welding wires: Understanding The Basics Of Welding Wire As a crucial part of the welding process, you, the reader, play a significant role in choosing the right welding wire. This thin, flexible metal rod serves as a filler material, joining two metal pieces together to ensure a strong bond. Your choice of welding wire, influenced by factors such as the type of metal you’re working with, the welding process you’re using, and the specific needs of your project, is instrumental in the success of your welding project. Types Of Welding Wire There are many types of welding wire, but the most common are MIG wire and TIG wire. Each has its own unique properties, applications, and benefits. 1. MIG Wire MIG stands for Metal Inert Gas arc welding. MIG wire is easy to use and versatile, which is why it is used in industrial and home welding projects. MIG welding uses a continuous solid wire electrode inserted into the weld pool through a welding gun, joining the two base materials. The process relies on a shielding gas, usually a mixture of argon and carbon dioxide, to protect the weld from contaminants present in the air. Types Of MIG Wire: Solid Wire: This is the most common type of MIG wire. It is best suited for welding thin materials such as mild steel and aluminium. It is known to produce clean and strong welds with minimal spatter. Most MIG welders use solid wire. Flux-Cored Wire: Also, unlike solid wire, flux-cored MIG wire has a flux core, which acts as a shielding agent. This eliminates the need for external shielding gas, making it ideal for outdoor welding or when the wind might blow away the shielding gas. Advantages of MIG Welding Wire When To Use MIG Wire: Versatility: One of the key advantages of MIG wire is its versatility. It’s an excellent choice for welding various metals, including mild steel, stainless steel, and aluminium. This versatility empowers you, the reader, to take on a wide range of welding projects with confidence and ease. Ease of use: Its straightforward process makes it popular for beginners and those working on small-scale projects. Good Speed: Mig welding is faster as compared to other methods. That is why it making more suitable for large projects 2. Tig Wire TIG wire, or Tungsten Inert Gas, is another popular welding wire known for its precision and clean welds. Unlike MIG welding, TIG welding wire uses a non-consumable tungsten electrode to create the weld. This precision and control inspire and motivate you, the reader, to master the art of TIG welding. Types Of Tig Wire ER70S-6: This is a common type of Tig wire used for welding mild steel. It offers good weldability and is known to create a clean, strong weld. ER308L: This wire is mainly used for welding stainless steel. ER308L Tig wire provides excellent corrosion resistance, making it ideal for projects requiring a high-quality finish. ER4043: This is an aluminium TIG wire known for its versatility and ability to create smooth, crack-resistant welds. Advantages of TIG Welding Wire: When To Use TIG Wire: Precision: TIG wire is ideal for projects that require a high level of precision, such as automotive work, aerospace applications, and custom manufacturing. Decorative Works: TIG welding is known for its clean, attractive welds, making it a preferred choice for visible or decorative welds. Variety Of Metals: You can use TIG wire to weld a wide range of metals, including stainless steel, aluminium, and copper alloys. When Choosing Welding Wire, Keep These Points In Mind: Simply selecting a welding wire for a project is not enough. Rather, choosing the right type of welding wire is important: Material Compatibility: Before choosing a wire for your project, make sure that the welding wire is compatible with the base material. Using the wrong wire can lead to a weak weld or even damage to the material. Wire Diameter: The thickness of the welding wire affects the weld’s strength and appearance. Thicker wires are suitable for thicker materials, while thinner wires work best on thinner materials. Shielding Gas: If you are using MIG wire, consider the shielding gas you need. Therefore, the gas mixture can affect the weld’s quality and the welding process’s ease. Project Environment: Consider whether you will be welding indoors or outdoors in a home or workshop. Because some wires, such as flux-cored MIG wire, are better suited for outdoor use where wind may interfere with the shielding gas. Welding Position: The position you will be welding in (flat, vertical, overhead, etc.) can affect the type of wire you choose. Also, Some wires perform better in specific situations, so choose the wire that fits your project. Difference Between MIG Wire And TIG Wire To effectively choose the best methods for your project, you need to know the difference between TIG welding wire Vs MIG welding wire. Power Source The power source makes a significant difference in the comparison between MIG and TIG welding. On the one hand, the power source for TIG welding can be AC or DC. Using any of the two power sources in TIG welding depends on the metal you want to weld and the type of electric arc you want. The AC power source is suitable for working with aluminium material, while the DC power source is suitable for stronger electric arcs. On the other hand, MIG welding uses a DC power source and the current is passed through the consumable wire to the workpiece. Metal Selection When it comes to TIG vs. MIG comparison in terms of metal
Choose Best Welding Rods & Welding Electrodes | Royal Arc Welding Supplies
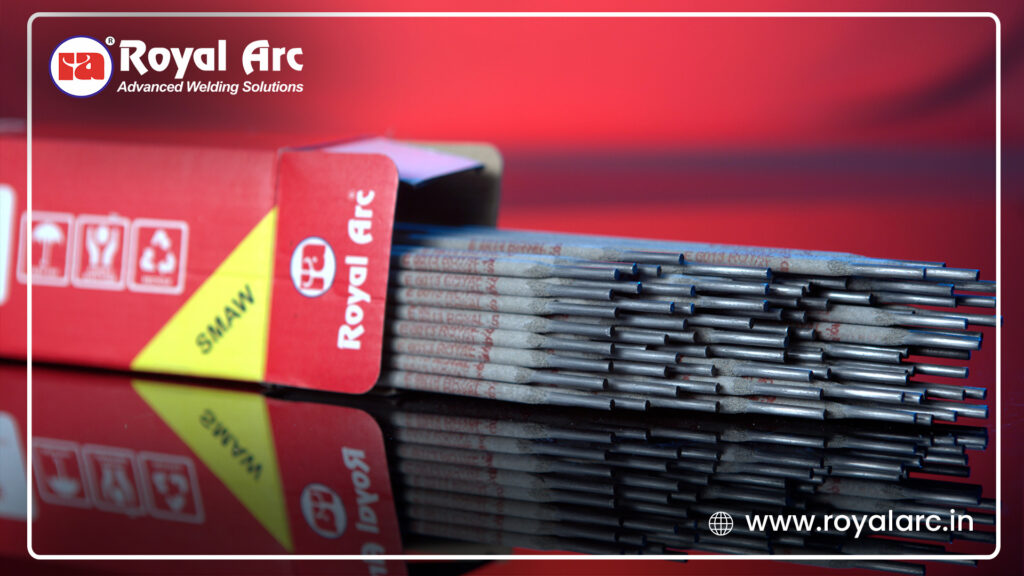
How to Choose the Best Welding Rod for Different Metal Types Welding, a process that involves joining metals by heating them until they melt and then allowing them to cool and fuse. It is a fundamental skill for beginners and professional welders. Understanding the various components of the welding process is crucial, and one of the most significant elements is the welding rod. This consumable plays a pivotal role in ensuring the quality of the weld, empowering you with the knowledge to create solid and stable joints. In this article, we will explore what a welding rod is, its types, and how to choose the right one for your project. So, let’s move on to the main topic: What is a Welding Rod? Welding rods, also known as electrodes, are welding materials that melt and flux during operations such as stick welding. To use a welding rod, you must first attach it to your welding equipment, creating an electric arc between the base metal and the welding rod. Because the electric arc is so intense, it quickly melts the metal, making it ready for welding. The base material, which is the part being joined, and the consumable, which is the material used to form the joints, are crucial in the welding process. Due to their shape, these materials, also known as base plates or tubes, flux-cored wire, consumable electrodes, etc., play a significant role in the welding process. Why are welding rods necessary? The right welding rod is not just a choice; it’s a crucial decision to make or break your project. It’s the key to achieving a strong, stable, high-quality weld. The type of welding rod used can affect various factors, such as the strength of the joint, the kind of metal being welded, and the appearance of the weld bead. For example, selecting a rod that matches the base metal is essential to avoid joint weaknesses or weld defects. Types of Welding Rods Several welding rods are available, each designed for specific techniques and metal types. Let’s take a look at some of the most commonly used welding rods in detail: 1. Mild Steel Welding Rods (E-6010, E-6011, E-6013) Mild steel welding rods are one of the most commonly used welding rods. They are versatile and easy to handle. They are suitable for most general-purpose welding tasks. These rods work well for welding low-carbon steel and provide high deposition rates. 2. Stainless Steel Welding Rods (E-308, E-309, E-316) Stainless Steel Welding Rods These are designed to weld stainless steel and other corrosion-resistant materials. They provide excellent resistance to oxidation and work well in high-temperature environments. 3. Cast Iron Welding Rods Cast iron rods are used to weld cast iron components. These are designed to prevent cracking, a common problem when welding due to the brittle nature of cast iron. Nickel-based rods are popular for cast iron applications because they produce strong, ductile welds. 4. Aluminum Welding Rods Aluminium welding rods are used for welding aluminium and its alloys. They are softer than other rods and require special handling to avoid contamination. They are ideal for repairing aluminium parts or creating lightweight structures. 5. Special Welding Rods Special welding rods include welding electrodes that are designed for specific applications. Hard-facing rods are used to apply welds to the surface of worn parts or in underwater welding. They are formulated to meet the unique requirements of particular welding environments. Factors to consider when choosing a welding rod Choosing the right welding electrode is crucial to the success of your project. Here are some points that can help you choose the right welding rod: 1. Base metal type The welding rod you choose should match the metal you are welding. For example, stainless steel rods are suitable for stainless steel metals, while aluminium rods are required for aluminium projects. 2. Welding position Some rods are designed for specific welding positions such as flat, horizontal, vertical or overhead. For example, E6010 and E7018 are versatile and suitable for various situations. 3. Joint design The type of joint and its accessibility also play a role in choosing the right rod. A thinner rod may be required if the joint is narrow or inaccessible. 4. Welding current Some rods are compatible with AC (alternating current), DC (direct current) or both. It is essential to ensure that the welding electrodes match the capabilities of your machine. 5. Desired weld characteristics Consider what you want the final weld to look like. Some rods create a smooth, shiny weld bead, while others create a rough finish. If aesthetics are important, choose a rod that provides the desired look. Conclusion Understanding welding rods and their applications is essential to produce high-quality welds. We read above how important it is to choose the right welding rod for your project. At the same time, selecting electrodes from the right company is most important for the success of your project. Quality welding rods from Royal Arc will be effective for all your projects.