Difference between MIG wire and TIG wire? Which welding wire is better for what?
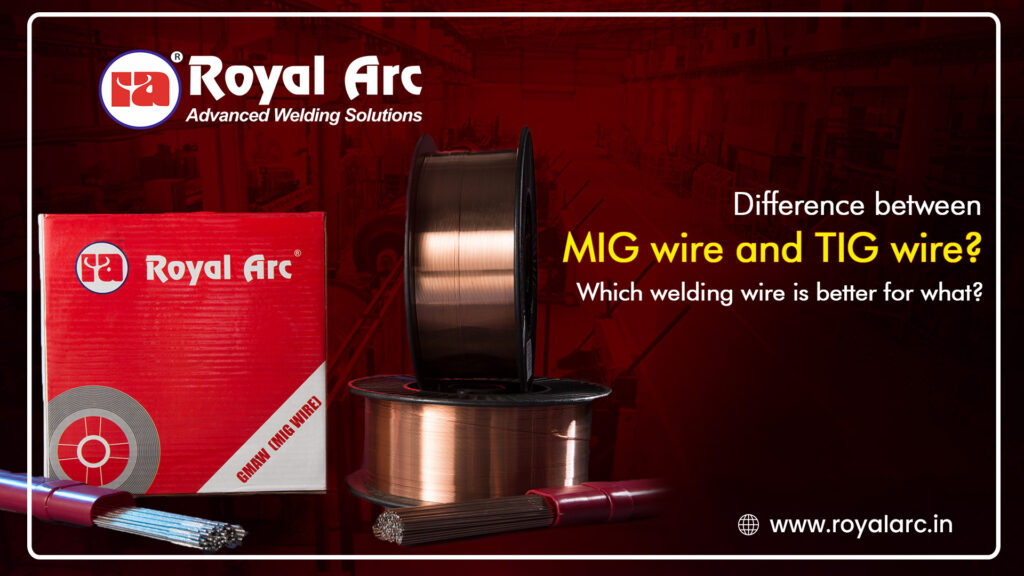
In today’s era, welding, a technique that has become the backbone of every industrial project, owes its success to professionals like you. Be it heavy machinery, automobile manufacturing, shipbuilding, railway bridges or precision medical equipment, your role in choosing the right Mig wire and Tig wire is crucial. Your decisions increase the quality of production and form the basis of safety and stability in every field. Welding wire is mainly of two types: Mig wire and Tig wire. The process, uses, and features of both of them are different. In today’s special article, we will learn about Mig Welding and Tig Welding, how they work, and which one is better suited for specific work. If you also want to know about this, then read this article till the end: What are Mig wire and Tig wire? Mig Wire (Metal Inert Gas Wire): The wire used in MIG welding is called MIG Wire, which is continuously fed through the welding torch by an automatic feeder system. MIG welding is also called GMAW (Gas Metal Arc Welding). This wire is wound on a spool and used with gas shielding (such as CO₂ or Argon). Features: Tig Wire (Tungsten Inert Gas Wire): The wire used in TIG welding is called TIG Wire. It is manually inserted into the welding pool by the welder. TIG welding is also known as GTAW (Gas Tungsten Arc Welding), which uses tungsten electrodes and pure Argon gas. Features: Use of MIG Welding Wire (MIG wire) MIG wire is used when there is a need for Major areas of use: Use of TIG Welding Wire (Tig wire) Tig wire is used when there is a need for: Major areas of use: Process and Technical Differences between Mig wire and Tig wire Parameter MIG Wire TIG Wire Wire Feeding Automated spool feed Manual rod feed Electrode Type Consumable Non-consumable (Tungsten) Shielding Gas CO₂ or Argon Pure Argon Speed Fast Slow, but controlled Skill Required Welds are possible with minimal skill Requires a high level of expertise Surface Quality Normal, sometimes with spatter Extremely clean and aesthetically finished Material Thickness Thicker metals like Mild Steel Thin and sensitive metals like Stainless Steel, Aluminium Production Application Mass production, like automobiles and infrastructure Custom fabrication like medical, decorative, and aerospace Based on these technical differences, it is decided whether MIG wire or TIG wire will be better for a particular project. Advantages and Disadvantages of MIG Wire and TIG Wire Advantages of MIG Wire 2. Easy to Learn: MIG Wire technology is simple for beginner welders as it does not require manual wire feeding. 3. Less Fatigue for Welders: Continuous wire feeding and arc control cause less fatigue to the welder. 4. Continuous Welding: Long and strong welds can be made without stopping, and joints are strong. 5. Versatility: It can also be used on carbon steel, stainless steel and aluminium with suitable gas shielding. Disadvantages of MIG Wire 1. Spatter Issues: MIG welding has more spatter. That’s why you spend extra time on cleaning and finishing. 2. Dependency on Shielding Gas: Wind in outdoor work can cause the gas shield to break, which can damage the weld on your project. 3. Limited to thin metals: Possibility of overheating and burning through on thin metals. 4. Less Attractive Welds: The finish of MIG is less clean and attractive than TIG. Advantages of TIG Wire 1. Superior Weld Quality: Welds made from TIG welding wire are clean, strong and of X-ray quality. 2. Excellent Aesthetic Finish: Extremely essential in decorative, food-grade and medical devices. 3. Great for Thin Metals: TIG welding has better heat control. This allows you to weld thin metals with precision. 4. Flux-free process: TIG has neither spatter nor slag. This is why you do not have to spend time cleaning. Disadvantages of TIG Wire 1. Slower Process: TIG welding is manual, which makes it slower than MIG. 2. Requires High Skill: TIG welding requires a uniform arc, manual wire feed and precise movement. 3. Expensive Setup: TIG welding machine, tungsten electrode and gas are all expensive. 4. Not Ideal for High Volume Production: Slow speed can be a hindrance for heavy construction and large volume welding jobs. Industrial Applications of MIG Wire and TIG Wire Industrial Uses of MIG Wire: Railway and Metro Projects: MIG wire is widely used due to its durability and high speed. Industrial Uses of TIG Wire: Why is Royal Arc the Best Choice? Conclusion Both Mig wire and Tig wire have their own characteristics and limitations of use. Choosing the right welding wire ensures the success, durability and safety of your project. If your requirement is high speed, large projects and easy use, then MIG wire will be suitable. On the other hand, if your priority is precision, beautiful finishing, and control over thin metals, then TIG wire will better suit your needs. Royal Arc makes your decision easy, as its wide range of both MIG and TIG wire provides high-quality results for your project. Behind every weld is the trust of Royal Arc for robust construction and long-term durability.