Welding Electrode Types And Their Uses | Royal Arc
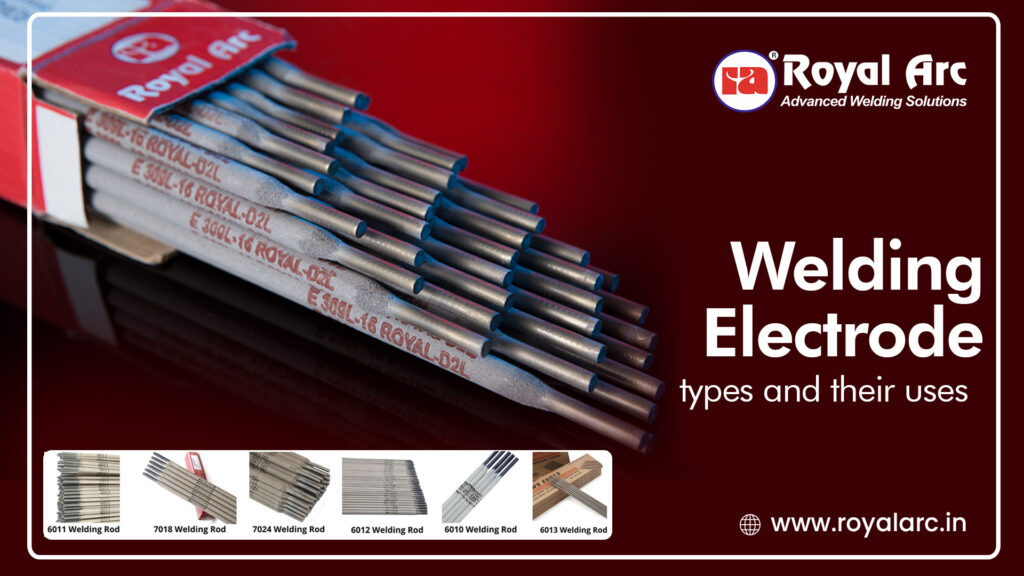
Welding electrodes, a cornerstone of the welding industry, play a pivotal role in joining metals and providing strength. Their correct identification and selection can significantly influence the quality of your welding project, underscoring their importance in your work. There are many leading welding electrode manufacturers in India, who produce high-quality electrodes. In this blog, we will discuss in detail the types of the best welding electrodes and their uses. So let’s move on to today’s main topic: What is a Welding Electrode? A welding electrode is a metal rod through which an electric arc is generated. It helps melt and join the metal surfaces. This gives a strong weld to your project. Welding Electrodes are Mainly of 2 Types: 1. Consumable Electrode These electrodes melt during welding and become a part of the weld. These are mainly used in SMAW, MIG, and SAW processes. 2. Non-Consumable Electrode These electrodes do not melt independently but are welded through a filler metal. They are majorly used in TIG welding. Types of Welding Electrodes and Their Uses 1. Mild Steel Electrodes Mild steel electrodes are the most commonly used welding electrodes. These are made of low carbon steel and are used in general construction works, pipeline installation, and the automobile industry. The main reason for their popularity is their low cost and easy availability. These electrodes give a stable arc and deep penetration to your project during welding. 2. Low Hydrogen-Type Electrodes Low hydrogen electrodes are best for applications with a high chance of cracking during welding. These electrodes keep the amount of hydrogen in the welding joint low, which maintains long-term strength in your project. You can use them in pressure vessels, bridge construction and pipe welding. Let me tell you that the quality and durability of the weld is extremely important here. 3. Low Alloy High Tensile Electrodes These electrodes are commonly used for welding high tensile metals. These electrodes are widely used in heavy structures, machinery, railway engines and shipbuilding. 4. Stainless Steel Electrodes Stainless steel electrodes are corrosion-resistant and perform well in high-temperature applications. These are commonly used in food processing, petrochemical, pharmaceutical and medical equipment manufacturing. Let me tell you that these electrodes produce corrosion-resistant welds during welding and are helpful in joining stainless steel surfaces. 5. Hard-Facing Electrodes Their main purpose is to harden the metal surface of your project and increase its lifespan. You can use Hard-Facing Electrodes for surfaces that have to withstand extreme friction and wear. These are used for welding in industrial machinery, mining equipment, agricultural equipment and heavy construction equipment. 6. Casting Electrodes Casting electrodes are specially designed to repair and weld cast iron. These electrodes are used in engine blocks, pumps, industrial machinery and casting manufacturing. You can use them when cast iron surfaces need to be joined or repaired. 7. Cutting & Gouging Electrodes These electrodes are used to cut metal and prepare smooth surfaces. These are especially important in applications where metal needs to be cut and shaped quickly. You can use these electrodes in industries like shipbreaking, automobile repair and metal fabrication. 8. Low Heat Input Electrodes You can use these electrodes in welding applications where excessive heat can damage the metal. These electrodes are specially made for welding thin metals. You can use low heat input electrodes mainly for electronics, jewelry manufacturing, and complex welding tasks. 9. Non-Ferrous Electrodes The primary purpose of non-ferrous electrodes is to make welding of lightweight and corrosion-resistant metals easier. You can use these electrodes to weld aluminum, copper, brass, and other non-ferrous metals. These electrodes play a vital role in the aerospace, automobile, electrical appliances and communication industries. How Do You Choose the Right Welding Electrode? As we have seen, the success of your welding project hinges on the electrode you select. Your expertise and knowledge in this field are crucial in making the right choice. Let’s delve into the key considerations when choosing the right welding electrode: Type of base metal Before welding, it is important to confirm that the welding electrode you choose is compatible with the base metal. Selecting the correct electrode according to the base metal type improves the weld’s strength & quality. For example, E7018 & E6013 are used for mild steel. Welding position You may be required to work in different positions as per the need during welding. For instance, you might need to weld in a vertical, flat, or overhead position. It’s important to remember that different types of welding electrodes are suitable for each position. Your attention to these details will improve the quality of the weld & reduce your positional challenges. Environmental conditions Your welding environment plays a vital role in electrode selection. Outdoor conditions, such as dirt & moisture, can impact the welding process. In such cases, E6011 welding electrodes, which perform well in these conditions, are recommended. High-quality low-hydrogen electrodes are ideal for indoor use for a clean and controlled environment. Conclusion Welding electrodes, a crucial part of the welding process, are designed for a wide range of applications across various industries. Their correct selection can significantly influence the quality and durability of the welding, making your construction work more safe and sustainable. The best Welding Electrode manufacturers in India, such as Royal Arc, offer high-quality electrodes that meet the diverse requirements of these industries, showcasing the versatility and applicability of your welding skills.
An Introduction to Flux Cored Wire: What You Need to Know
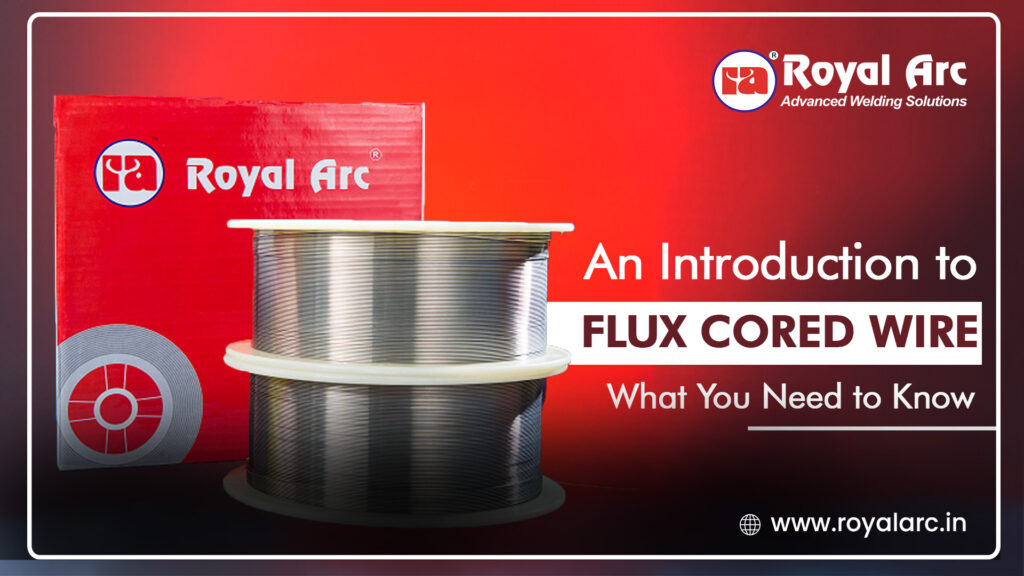
Flux Cored Wire, a crucial component in the welding industry, offers numerous benefits over traditional solid wire. Its versatility makes it particularly suitable for heavy industrial and construction work. With leading Flux Cored Wire Manufacturers in India producing high-quality products designed to meet the needs of various industries, this blog is a must-read for those seeking a detailed understanding of Flux Cored Wire. In this blog, we will learn the uses of Flux Cored Wire, and its manufacturing process. Apart from this, how is Flux Cored Wire different from other types of welding wire? We will discuss this in depth. What is Flux Cored Wire? Flux Cored Wire stands out as a special type of welding wire, distinguished by its hollow structure filled with flux. Available in both gas-shielded and self-shielded forms, it is versatile and applicable in a wide range of welding scenarios. Its primary function is to enhance the effectiveness and efficiency of the welding process. Structure of Flux Cored Wire. The unique structure of flux cored wire, as mentioned earlier, is characterized by a hollow metal wire filled with a special type of flux. This flux serves the crucial function of protecting the weld from oxygen and moisture, thereby enhancing the quality of your welding. The structure of flux-cored wire mainly consists of the following elements: Difference between Flux Cored Wire and other Welding Wires. Flux Cored Wire is different from other welding wires like MIG Wire and Stick Electrodes. Gas Protection: Flux Cored Wire can provide shielding automatically due to its flux. MIG Wire requires a separate shielding gas. Better penetration and less spatter: Flux Cored Wire can weld to greater depths and produce less spatter. This results in a stronger weld on your project. Multi-positional welding: Flux Cored Wire can be used in vertical, horizontal, and overhead welding. This enables better weldability. Effective in outdoor conditions: This works even in the air. Whereas MIG Wire requires shielding gas. Types of Flux Cored Wire. Flux Cored Wire is usually divided into two main categories: Gas Shielded Flux Cored Wire: It works with shielding gas such as CO2 or Argon. Gas Shielded Flux Cored Wire provides better weld quality and less spatter. It is used in heavy structures, shipbuilding and the automotive industry. Self-Shielded Flux Cored Wire: It does not require additional shielding gas. In addition, Self-Shielded Flux Cored Wire works better in outdoor environments. It is generally used in construction sites and welding works at height. Applications of Flux Cored Wire: Flux Cored Wire is used in various industries, including: How to choose the right Flux Cored Wire? Why Choose Royal Arc? Expertise: Royal Arc has years of experience and technical knowledge. Years of experience make it the leader in Flux Cored Wire manufacturing. Complete Product Catalog: We have a wide range of Flux Cored Wire available to meet your various industrial requirements. Unparalleled Quality: Flux Cored Wire manufactured by Royal Arc follows high-quality standards. Therefore they are reliable and efficient. Conclusion: Flux Cored Wire is a revolutionary product in the welding industry. It provides more efficiency than traditional welding wire. Its various types, applications and benefits make it indispensable in the industrial sector. If you want high quality and reliability, then Royal Arc is the right choice for you.
Welding Rod Types: What Are They And Their Various Uses?
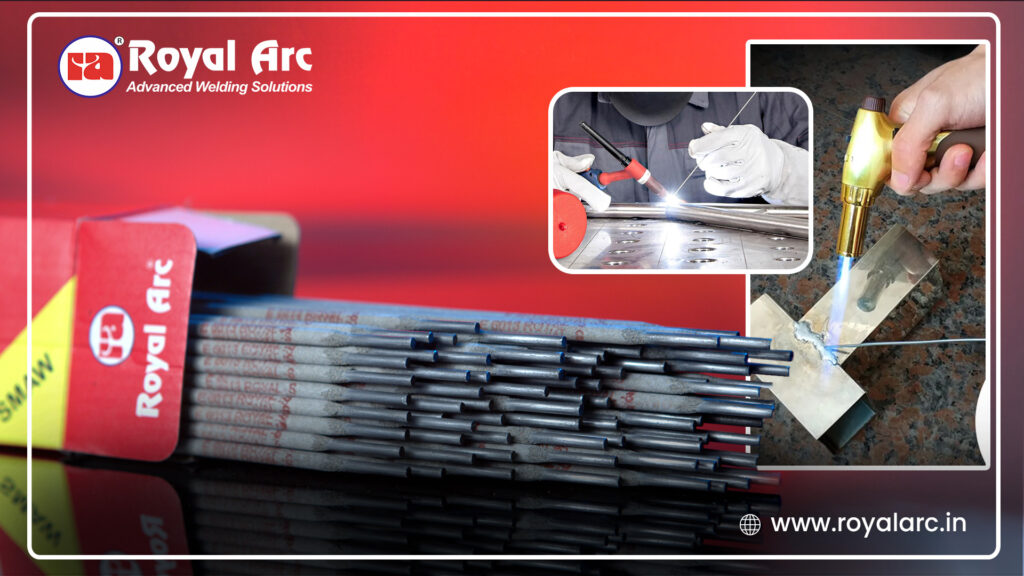
Welding technology has revolutionised modern industries and manufacturing processes. One of the most versatile elements in this field is the welding rod, also known as a welding electrode. The rod’s adaptability and usefulness across various applications make it a pivotal player in joining a wide array of metals in welding. In this blog, we will discuss in detail the types of welding rods, their features and the use of welding electrodes. So, let’s move on to the main topic: What is a Welding Rod? A welding rod is an important part of the welding process. It is a metal rod or wire that joins two metal pieces. The metal is heated and melted through the welding rod, creating a strong and durable joint. The choice of a welding rod depends on your welding process and the type of material. Types of Welding Rods There are different types of welding rods. Welding rods are selected based on the requirements of your project, metal type and welding technique. Let’s know about welding rod types: 1. Consumable Electrodes Consumable electrode welding rods act as a filler material between the metals being joined by melting during welding. They can be mainly divided into two categories: SMAW (Shielded Metal Arc Welding) SMAW Welding rods are coated with flux, which protects the metal from oxidation in the welding process. They are mainly used in pipelines, bridges and heavy structures. GMAW (Gas Metal Arc Welding) GMAW, also known as MIG (Metal Inert Gas) welding, uses the rod as a continuous wire. It is suitable for fast and effective welding in the automotive and construction industries. 2. Non-Consumable Electrodes Non-consumable electrodes don’t melt during welding. They only create an arc and heat the welding area. The most common type is the tungsten electrode, which is used in TIG (Tungsten Inert Gas) welding. It is typically used in areas where weld quality and accuracy are important, such as the aerospace and petrochemical industries. 3. Bare Electrodes Bare electrodes are simple metal electrodes without any coating. It is used in those works where no kind of flux is required in welding. These rods are generally suitable for light and clean welding. They are mainly used in small repairs and machine maintenance. 4. Coated Electrodes Coated electrodes have a thin layer of flux on them, which is a chemical compound that protects the metal during the welding process. Flux prevents oxidation of the weld and forms a protective layer. They are suitable for a variety of welding positions like vertical and horizontal. Coated electrodes are used in large construction works, bridge construction and heavy machinery. 5. Flux-Cored Electrodes These electrodes are empty from the inside and filled with flux. Flux-cored Wire electrodes provide additional safety and stability for welding. They can be used with CO2 or other gases. They are generally used in shipbuilding and pipeline projects. 6. Stainless Steel Electrodes These electrodes are used for stainless steel welding. Stainless Steel Electrodes help make corrosion-resistant, high-quality welds. They are mainly used in the food, chemical plants, and marine industries. 7. High-Heat Resistant Electrodes These electrodes are specially designed for situations where the weld has to resist extreme heat, such as in power generation, boiler manufacturing, and high-temperature equipment like furnaces and kilns. They maintain their structure and strength. High-Heat Resistant Electrodes are mainly used in these industries. Uses of Welding Rods 1. Construction Industry Welding rods are indispensable in the construction sector, where they are used extensively to build bridges, structures, and buildings. Notably, E6013 and E7018 welding rods are used extensively in this industry. 2. Automotive Industry The automotive sector relies heavily on welding rods to join parts and bodies. TIG and MIG welding rods are particularly popular in this industry. 3. Aerospace Industries The aerospace industry demands lightweight yet robust welding, which requires special non-ferrous and TIG welding rods. 4. Petrochemical Industry Stainless steel welding rods and flux-cored welding rods are used to weld pipelines and tanks. These rods are the best solution because of their high temperature and chemical resistance. 5. Shipbuilding Industry Rods used in shipbuilding such as flux-cored welding rods and submerged arc welding rods are suitable for strong water-tight welding. 6. Energy Production Stainless steel and submerged arc welding rods are used more in power plants and renewable energy projects. 7. Food and Beverage Industry Stainless steel welding rods are mainly used in the Food and Beverage Industry. They make the welding joints completely hygienic and corrosion-resistant. 8. Pipeline Industry Oil and gas pipelines use cast iron and flux-cored welding rods, which can withstand high pressure and temperature. Tips for Selecting Welding Rods Metal Compatibility: Choose the welding rod according to the metal you want to weld. Understanding the welding process is crucial; it’s the process: the right welding rods. This knowledge enables you to make informed decisions, ensuring the success of your welding project. Thickness and Size: Correct welding rod size and thickness improve welding performance. Performance requirements: Select a suitable welding rod for high temperature and pressure. Conclusion Welding rods are not just materials, they are the backbone of every successful welding project. Choosing the right rod is the key to ensuring the quality and durability of your welding. Whether it’s the construction industry, the automotive sector, or the plumbing industry, the right use of welding electrodes guarantees a job well done. Royal Arc is a leading manufacturer of welding rods and wires in India. Our high-quality products are designed to meet every type of welding requirement.
Applications of Welding Wire in Various Industries| Royal Arc
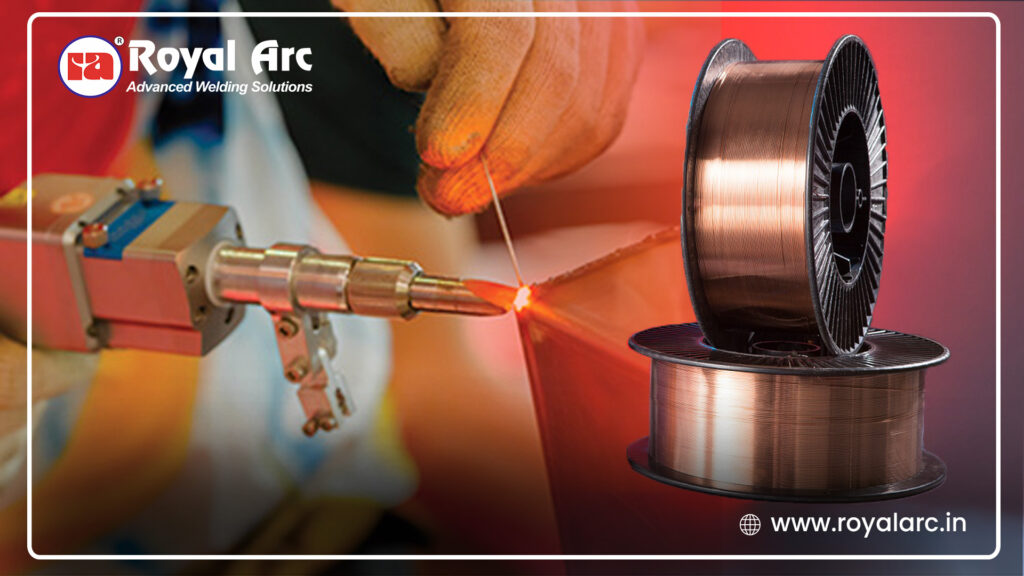
Welding wire plays an important role in today’s modern industries. It is an important consumable material in various welding processes such as Mig Wire, Tig Wire and Arc, and Welding Wires. The right selection of welding wire improves your welding results and ensures welding quality and durability. In this blog, we will understand the types of welding wire and their applications in detail. Let’s move on to the main topic: What is Welding Wire? Welding wire is a wire of metal that acts as a filler material during welding. It is available in different types and sizes according to the welding process. With the help of welding wire, a strong and durable bond is created to join two metals. Types of Welding Wire 1. Mig Wire MIG welding wire is mainly used in Gas Metal Arc Welding (GMAW) processes. It is suitable for steel, mild steel, and other metals and is ideal for automatic and semi-automatic welding. 2. Tig Wire TIG welding wire is used in tungsten inert gas (TIG) welding. It is useful for metals like stainless steel, aluminium, and other non-ferrous metals and is ideal for high-quality, precision welds. 3. Flux Cored Wire Flux-cored wire has a coating that creates shielding gas while you are welding. This wire is useful in situations where shielding gas is not available. 4. Arc Welding Wires Arc welding wire is used in manual welding processes. It is generally useful in applications requiring a strong and durable bond. 5. Specialty Wire Welding wire designed for special applications, such as high-temperature or cryogenic welding, comes with special materials and coatings. It is used in very few places Applications of welding wire in different industries Welding wire has become an essential part of modern industries. With its help, your work of joining two metals becomes simple, strong and durable. Its requirements and use are different in different industries. Correct use of welding wire increases production efficiency and also ensures construction quality. Let us know in which industries and how welding wire is used: Automotive Industry Welding wire is of significant importance in the automobile industry. Generally, MIG and TIG wire are used to connect vehicle chassis, body panels and engine parts. With the help of welding wire, lightweight but strong bonds are created, making the structure of vehicles strong, durable and safe. In addition, with the help of MIG wire, your production process is fast and accurate. Aerospace Industry The aerospace industry is one of the most important industries. It uses light and strong metals, which require a high-quality welding process to join them. TIG wire is the most suitable welding wire for this industry, as clean and precise welding is very important. The welding wire is used to join the wings, fuel tanks, and other important parts of aeroplanes. The quality of the welding wire has a direct impact on the safety and performance of the aeroplane. Construction Industry In the construction industry, welding wire is used to build buildings, bridges, and other structures. Generally, MIG wire and flux-cored wire are used to join large structures. This industry requires a strong and durable bond, which welding wire achieves. It is also used to join steel beams and pipelines and repair heavy equipment. Petrochemical Industry In the petrochemical industry, flax cord wire and the arc welding trade are used to weld heavy equipment, tenons, and papillae. This industry generally works in harsh conditions, where the welder has to endure high temperatures, pressures, and the effects of chemicals. Flax cord wire performs excellently under these conditions and provides a strong bond to your project. Shipbuilding Industry In shipbuilding, the welding trade is used to join heavy steel platens and pipelines. MIG and Flax Cored Wire play a major role here. Generally, the safety of the ship is ensured in the shipbuilding process, as the safety is fixed in the shipbuilding. Apart from this, the welding business is also used to repair damaged parts of the ship. Energy Production Welding wire connects important devices in energy production, such as power plants, wind turbines and solar systems. Generally, TIG and MIG wire are used here. There are possibilities for welding boilers, turbines and boilers in power plants with high-quality welding wires. Pipeline Industry Welding wire is widely used in the pipeline industry to connect and repair large pipelines. Flux-cored and arc-welding wires are also widely used. Generally, welding wire is designed to withstand high pressure and temperature. It is also used to ensure the safety and durability of gas and oil pipelines. Things to consider while choosing a welding wire Type of metal: Choosing the right welding wire depends on the compatibility of the metal. Wire size: Choose the right size and thickness of the welding wire as per the welding requirement. Availability of shielding gas: MIG and TIG welding wires require shielding gas. Welding position: Some welding wires are designed for specific welding positions. Conclusion Welding wire plays an essential role in various industries. Choosing the right welding wire makes welding easier and improves welding quality. Whether you are in the construction, automotive, or aerospace industry, using the right welding wire is crucial to the success of your project. Royal Arc is the most reliable choice for you if you are looking for high-quality welding wire. Royal Arc is a dedicated welding wire manufacturer in India. It offers high-quality products, including a wide range of MIG, TIG, and arc welding wires. Our welding wires are ideal for mild steel and other metals.
Understanding Different Types of Welding Consumables | A Comprehensive Guide
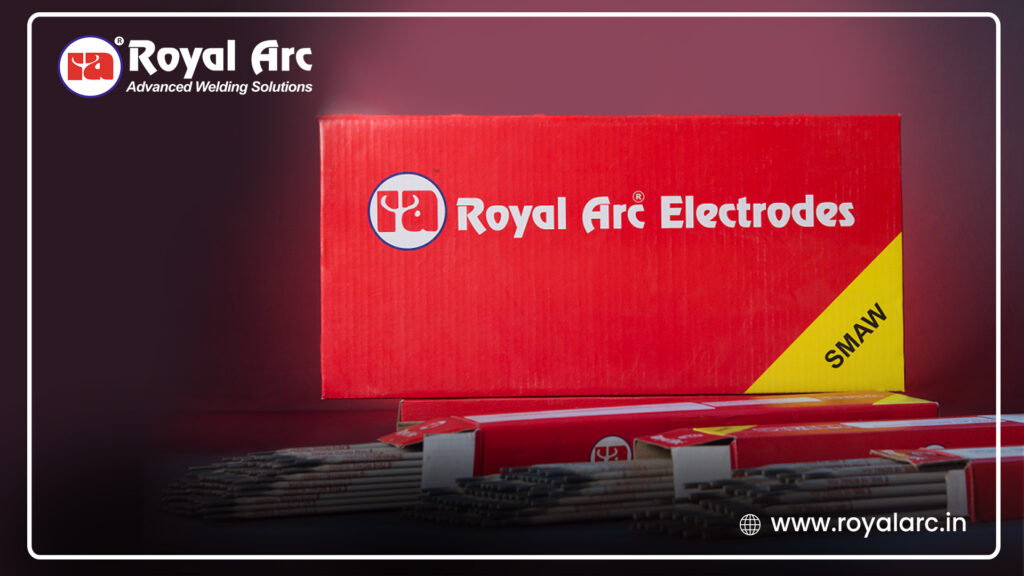
Welding is essential in the construction, repair, and engineering industries. Its success depends on the right consumables, which are materials consumed during the process to ensure the quality of the weld. This blog will detail the different types of welding consumables and their uses. So, let’s move on to the main topic: What are welding consumables? Welding consumables are materials that help create a weld during the welding process. These include welding electrodes, flux-cored wire, MIG/TIG welding wire, and flux. These materials are essential for the strength, durability, and performance of your weld. Choosing the right consumables is vital to an efficient welding process. Types of Welding Consumables Here, we will understand the different types of welding consumables in detail: 1. Welding Electrodes Welding electrodes are one of the most common welding consumables. Welding electrodes are generally classified into two types: (i) Consumable electrodes melt during welding, joining the weld and becoming part of the weld material. They are generally used for welding mild steel, stainless steel, and cast iron. They are also used in shielded metal arc welding (SMAW) and gas metal arc welding (GMAW). Examples include electrodes like E6013 and E7018. (ii) Non-Consumable ElectrodesThese electrodes do not join the weld like tungsten electrodes, generally used in TIG welding. Non-consumable electrodes can tolerate more heat and last longer. 2. Flux Cored Wire Flux-cored wire is an advanced welding material that contains flux inside the wire. It is suitable for heavy welding tasks and automation. It protects the weld and makes the welding process more manageable. Flux-cored wire suppliers in India offer a wide range of wires suitable for mild steel, stainless steel, and other metals. Flux-cored wire ensures accurate welding, has a high deposition rate, and can be used even in poor environmental conditions. Example: Best Flux Cored Wire for Mild Steel includes products like ROYALFIL GS 12 R. 3. MIG Welding Wire / TIG Welding Wire The wires used for MIG welding and TIG welding help produce high accuracy and neat welds. i. MIG Welding WireMIG Welding Wire is the best for mild steel, stainless steel and aluminium welding. It is used in automotive, construction and industrial applications. ii. TIG Welding WireTIG welding wire is used for stainless steel, aluminium, and other light metals. It is essential for neat welds and is generally used to join light metals and thin sheets. Mig/Tig welding wire suppliers in India offer various grades and size options to meet every type of welding requirement. 4. Flux Flux is a unique powder or coating that protects the weld from oxidation and contamination. It produces a gas during welding that shields your weld. Flux is mainly used in electrodes and flux-cored wires. The two main types of flux are Solid Flux and Paste Flux. 5. Welding Filler Metals This metal is used to fill the gap in the weld. Generally, different types of filler metals are available for stainless steel, carbon steel, and alloy steel. How do you choose welding consumables? Choosing the right welding material is essential to maintain welding quality. Choosing the wrong material can lead to weld weaknesses and project failure. The right welding material can determine the success of your job. That is why your welding material is important in many ways. Therefore, you must buy welding materials from India’s best welding electrode manufacturers. Let us know what points should be kept in mind while selecting welding consumables: Metal Type Different welding consumables exist for mild steel, stainless steel, and aluminium. For example, the Best Flux Cored Wire for Mild Steel is suitable for mild steel welding. Similarly, the choice of welding consumable depends on the metal. Welding position It is essential to select the right consumable material for the situation during welding. Different materials are required for flat, vertical, and overhead welding. Environmental conditions Indoor welding and outdoor welding require different types of welding consumables. Required performance Select high-quality materials, such as High-Quality Welding Electrodes, for greater strength and durability. Conclusion Welding consumables are crucial to the success of the welding process. We read above that choosing the right material enhances the quality of your project’s welds and ensures safety. At the same time, choosing the wrong material can deteriorate the quality of your project’s welds. It is essential to consider the base metal, welding process, environmental conditions and standards while selecting welding consumables. Royal Arc is a top welding consumables manufacturer in India that provides high-quality solutions for all your welding needs. It is the best welding company in India for all your needs. Choosing the right material ensures the success and durability of your projects.
An Intro to Flux Cored Wire: Key Facts You Should Know – Royal Arc
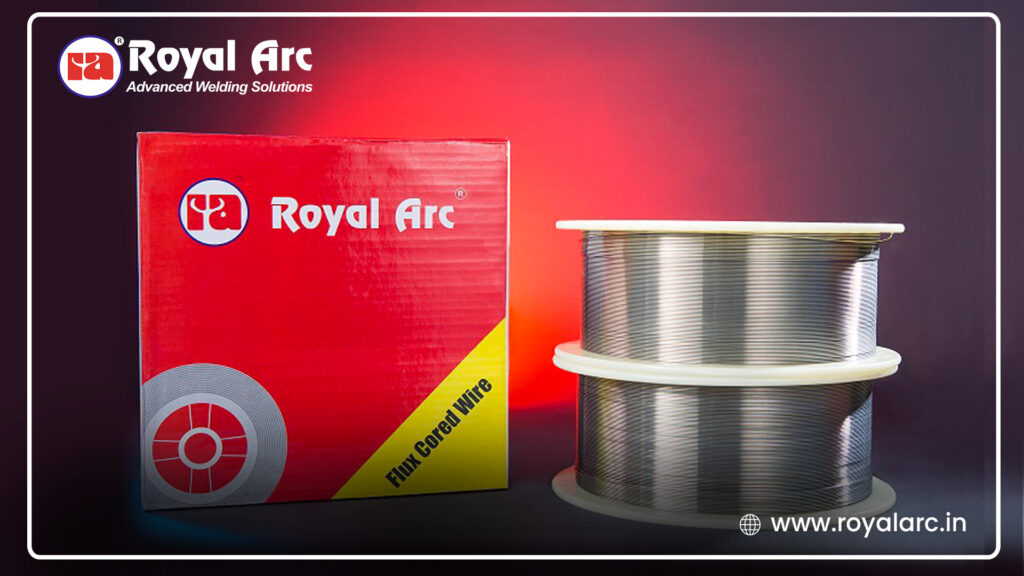
Various materials are used in the welding industry to enhance welding quality. One of them is flux-cored wire. Flux cored wire, a special type of welding material, is gaining traction in the industry, evident from its increasing demand. Its use not only simplifies the welding process but also makes it more effective. In this blog, we will delve into the details of what flux cored wire is, how to select the Best Flux Cored Wire for Mild Steel, and most importantly, why it is crucial to choose the right Flux Cored Wire Manufacturers in India. This information will guide you in making the best choice for your welding needs. What is Flux Cored Wire? Flux-cored wire is a special type of welding wire used in the FCAW (flux-cored arc welding) process. It has a core inside the wire that is filled with flux. FCAW flux produces a shielding gas during welding, protecting the wire from dirt, moisture, and oxidation. This wire, usually manufactured according to Flux Cored Wire Specifications, is versatile and can be used in a variety of welding applications, further enhancing its value. Importance of Flux Cored Wire Flux-cored wire has made its mark in the field of welding. FCAW makes your welding process easier and gives durable results. During welding, this flux generates gas when exposed to heat, which protects the weld from oxidation and other harmful elements. This wire is very effective in the welding process. It helps your project achieve excellent strength. It is useful in all types of welding situations, whether flat, vertical, or overhead. Using flux-cored wire reduces welding time and effort, thereby increasing production rates. Types of Flux Cored Wire Flux-cored wire is available in two major types: Self-Shielded Flux Cored Wire This type of flux-cored wire is used without additional shielding gas. It is generally best for outdoor welding and strong windy conditions. Dual-Shield Flux Cored Wire Dual-Shield Flux Cored Wire uses shielding gas. This second type of flux-cored wire is suitable for high-quality welding and controlled environments. Uses of Flux Cored Wire Flux-cored wire is used in various industries, such as: Construction Flux-cored wire plays an important role in construction. Its strength and accuracy allow even big projects to be successfully completed. Flux-cored wire is used for building construction, bridge construction, and welding heavy machinery. Mild Steel Welding Flux-cored wire is usually used to join mild steel structures, which is why it is called the Best Flux-Cored Wire for Mild Steel. Repair and Maintenance In the welding industry, flux-cored wire is very important in repairing broken parts and old structures. Its use increases the quality and efficiency of the weld. Automobile Industry Flux-cored wire is also used in vehicle manufacturing and repair. Advantages of Flux Cored Wire There are many advantages of using flux cored wire: Better quality: The quality of welding is improved due to the flux. Time-saving: It provides a faster and easier welding process. This saves you time. Useful in all positions: Flux-cored wire is equally effective in flat, vertical, or overhead welding, so it can be used in all positions. Less cleaning required: The slag can be easily removed after welding, creating less mess and requiring less cleaning. Ideal for outdoor welding: The self-shielded type performs well without shielding gas. Selection of Flux Cored Wire Choosing the right flux cored wire is crucial for the success of your project. Understanding the specific requirements of your welding task and selecting the appropriate flux cored wire will empower you to achieve the best results. Moreover, you need to select flux-cored wire according to the type and condition of welding. If you are working in an outdoor environment, self-shielded flux-cored wire can be a good option. At the same time, for high quality and accuracy, you should use dual-shielded flux-cored wire. The diameter of the flux-cored wire is also an important factor. It depends on your welding depth and material thickness. Selecting the right flux-cored wire makes your welding process easier and also increases the quality of the weld. Flux Cored Wire Manufacturers Royal Arc, a reputed manufacturer of Flux Cored Wire in India, is a name synonymous with reliability and excellence in the field. All our products are manufactured to adhere to international standards and meet all customer requirements. When it comes to finding the right wire for welding, you can trust Royal Arc’s Flux Cored Wire Manufacturers in India to deliver quality and performance. Conclusion Flux Cored Wire has become an indispensable tool in the welding industry. Its features and advantages make it the most suitable choice for welding. If you want quality, efficiency and durability in welding, use flux cored wire from Royal Arc. It will simplify your welding process, increasing productivity and performance. If you are looking for the correct wire for the Best Flux Cored Wire for Mild Steel or other materials, contact Royal Arc today.
Benefits of Using High-Quality Welding Electrodes | Royal Arc
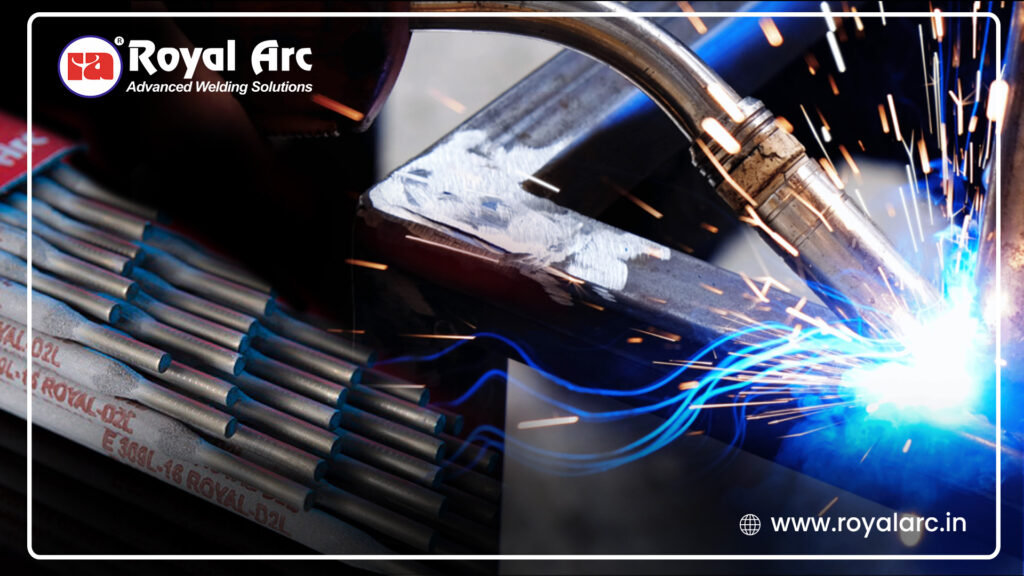
In the welding industry, making a strong and durable weld is important. Choosing the right welding electrode according to the material is even more important. Welding electrode, also commonly called stick or rod. It is an integral part of the welding process. Using high-quality welding electrodes increases the weld’s strength, saving cost and time. This blog will explain why high-quality welding electrodes should be used. And what are its advantages? So, let’s move towards the main topic: What is a welding electrode? A welding electrode is a metal rod used to join two metals during the welding process. The rod melts to form fusion, thereby strengthening the weld joint. A flux coating on the outer surface of the electrode protects the weld from delamination and oxidation. Benefits of using high-quality welding electrodes 1. Strong and durable welds The most significant advantage of high-quality welding electrodes is that they provide solid and durable welds. Poor-quality electrodes create weak joints that do not last long. 2. Perfect welding performance High-quality electrodes provide better arc stability, making the welding process easier and more efficient. They also generate less spatter and reduce cleaning work. 3. Saves time and cost Better quality electrodes save both your time and cost. You have to repair weak welds again. Using the best welding electrodes for mild steel gives a strong weld, which completes your work quickly and correctly. 4. Suitable for various metals High-quality welding electrodes are compatible with various metals, such as stainless steel, carbon steel, and aluminium. If you are looking for the right option for mild steel welding, choosing high-quality electrodes is a must. 5. Performance in Environmental Conditions Good-quality electrodes perform well even in sunlight, humidity, rain, dust, and other harsh conditions. This is especially important when you are working on outdoor projects. How do you choose the right welding electrode? As we’ve seen, the success of your welding project hinges on the welding electrode you select. Let’s delve into the key considerations when choosing the right welding electrode: Type of base metal Before welding, it is very important to confirm that the electrode you choose is compatible with the base metal. Selecting the correct electrode according to the base metal type improves the weld’s strength and quality. For example, use E6013 or E7018 for mild steel. Welding position You may be required to work in different positions as per the need during welding. Such as flat, vertical, or overhead position. It’s crucial to remember that different types of electrodes are suitable for each position. Your attention to these details will improve the quality of the weld and reduce your positional challenges. Environmental conditions Your welding environment plays a crucial role in electrode selection. Outdoor conditions, such as dirt and moisture, can impact the welding process. In such cases, E6011 electrodes, which perform well in these conditions, are recommended. For indoor use, high-quality low-hydrogen electrodes are ideal for a clean and controlled environment. Best Welding Electrodes for Mild Steel Selecting the correct welding electrode for mild steel ensures the quality and strength of the weld. 1. E6013 Electrode E6013 is a general-purpose electrode that produces smooth and clean welds. It is suitable for welding in flat and vertical positions. You can use it in light construction and repair works. 2. E7018 Electrode This low hydrogen electrode is mainly used to create solid and crack-resistant welds. You can use E7018 in heavy construction projects with mild steel. 3. E6011 Electrode It is designed for deep penetration. E6011 works well outdoors and on rusted surfaces. Selecting the appropriate electrode depends on your project needs and the thickness of the mild steel. Conclusion Using high-quality welding electrode enhances the quality and durability of your project’s welding. They give your project strong, clean welds and also save time and cost. If you want the best option for mild steel welding, consider high-quality electrodes like E6013 and E7018. Royal Arc welding electrode manufacturers in India provide many affordable and reliable options. Choose the right electrode from Royal Arc according to your project needs and give your project a strong grip by welding.
Shielded Metal Arc Welding (SMAW) Guide | Master Welding with Royal Arc
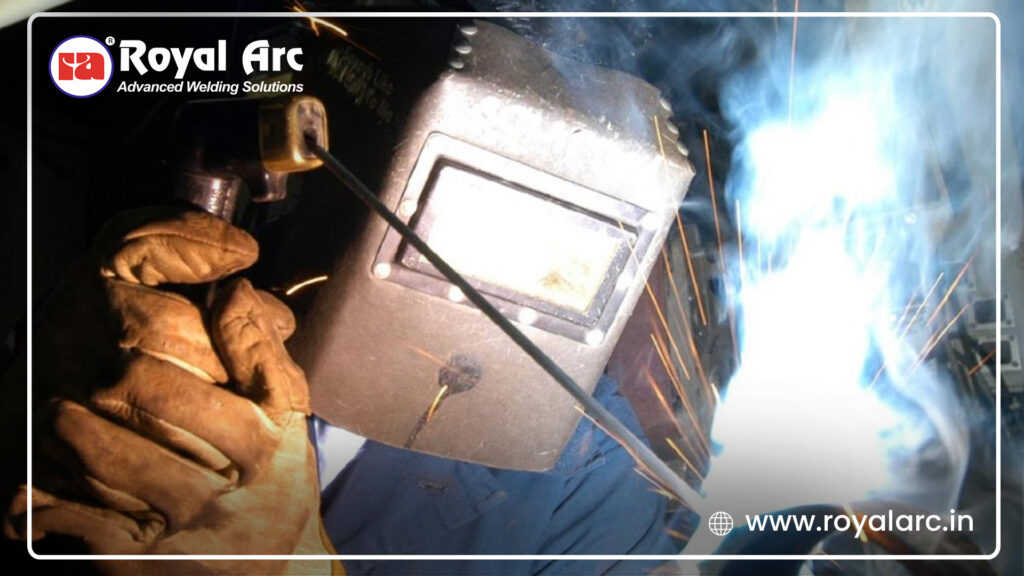
Shielded Metal Arc Welding (SMAW) is a popular welding technique. It plays a very important role in the way work is done on different types of projects. Due to the simplicity and durability of SMAW Welding, it is used for small repair work to large industrial projects. In this special blog, we will discuss in detail the types, features, uses, and advantages of Shielded Metal Arc Welding. So, let’s move towards the main topic: What is Shielded Metal Arc Welding (SMAW)? In 1888, Nikolay Slavyanov invented the consumable metal electrode for welding. Shielded metal arc welding (SMAW) is a type of arc welding. It uses a flux-covered electrode to join two metal pieces together. The electrode has a flux covering, which provides shielding gas to protect the weld area from atmospheric contamination. The melted metal also forms a slag on top of the weld and protects it. After welding, the slag is removed using a chipping hammer and wire brush. Working Principle of Shielded Metal Arc Welding It works on the principle of heat generated by an electric arc. The heat produced by a consumable flux-coated electrode is used to melt the base metal and fuse it together to form a strong weld joint. It uses a flux-coated electrode which melts and acts as a filler material. Main Parts of Shielded Metal Arc Welding: Power Supply A constant current output power supply is used in the Smaw Welding process, which provides constant (and never-changing) current during welding, even in the case of changes in arc distance and voltage. Electrode Consumable type electrodes with flux covering are used in SMAW. The electrode gives off vapours known as shielding gas and slag during the welding process. The shielding gas protects the weld area from atmospheric contamination and the slag deposited on the molten metal. It prevents the metal from coming in contact with atmospheric gas, protecting it from oxidation (contamination). The selection of electrodes in shielded metal arc welding depends on various factors. Electrode Holder It is used to hold the electrode in the desired position for welding. Welding Cables or Leads These are the cables used to connect the electrode and the workpiece to the welding power supply. They are also called leads. Ground Clamp This is attached to the workpiece, and the other end is connected to the welding power supply terminal through a welding cable. This completes the circuit, and the current starts flowing. Types of Shielded Metal Arc Welding SMAW can be divided into different types based on the welding rods and electrodes used. Such as: E6010 Electrode E6013 Electrode E7018 Electrode Stainless Steel Electrodes Features of Shielded Metal Arc Welding Less equipment required: In this process, you need a welding machine, electrodes and a welding helmet. For this reason, it is a cheap and easy option. Multi-position welding: SMAW can be used in flat, vertical, horizontal and overhead positions. No need for external shielding gas: The flux-coated rod provides the necessary shield to the weld. That is why you do not need external shielding gas. Advantages of Shielded Metal Arc Welding Where is Shielded Metal Arc Welding used? 1. Industrial construction and structures SMAW is used in buildings, bridges, and large infrastructure projects. It is perfectly suitable for creating strong welds. 2. Pipeline welding SMAW is used in pipeline installation and repair. Electrodes like E6010 are considered ideal electrodes for plunging into the pipeline. 3. Repair and maintenance SMAW is a perfect option for repairing broken machinery parts. Let me tell you, it is also used to rebuild shaft rollers, guide rolls, and chain rollers for heavy vehicles and industrial equipment. 4. Marine industry SMAW is used for welding the deck and engine parts of ships Smaw Welding Royal Arc is the best choice for you if you are looking for high-quality welding rods for your welding projects. Our Shielded Metal Arc Welding (SMAW) range offers a wide range of stick electrodes. These are the ideal electrodes for any industrial or repair work. Royal Arc products provide durable, strong and reliable welds.
Flux-cored wires – Know about their types and applications
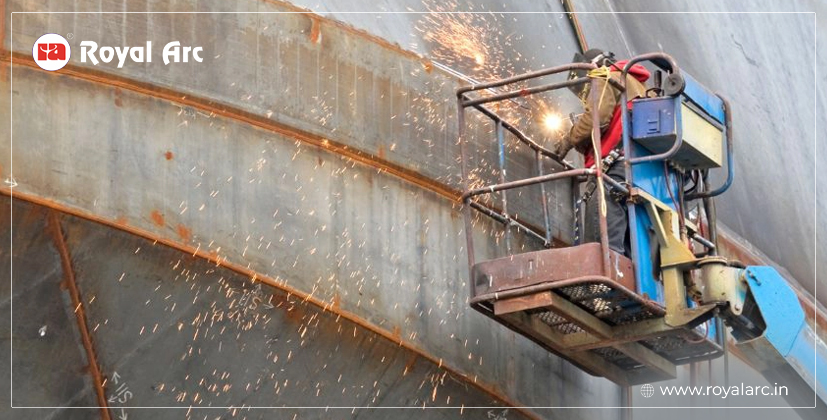
FCAW or flux-cored arc welding is a subcategory of MIG welding. As the name implies, this technique uses a flux-cored electrode that provides filler material for the weld. Flux-cored arc welding is a viable technique for heavy applications. Flux-cored welding wire manufacturers offer welding consumables for various purposes. Some of them include heavy equipment repair, structural steel erection, and bridge construction. The convenience and best result of flux-cored bring a more productive and cost-effective solution. Flux Core Welding Method Flux core welding is termed as tubular electrode welding which evolves from MIG welding. It is an arc welding process in which welders provide heat for welding by an arc formed between a fed tubular electrode wire and the work material. It helps in enhancing arc action, weld metal properties, and weld appearance. The shielding process uses the flux contained within the tubular electrode wire or through the flux and an externally supplied shielding gas. Figure 10-55 depicts a flowchart of the process. A flux-cored welding wire is also termed as an electrode. It is a hollow tube that contains a mixture of fluxing agents, deoxidisers, metal powders, and ferroalloys. The closure seam is the only notable change between the solid cold-drawn wire and flux-cored wires. Cored welding wire manufacturers provide two methods for welding with flux-cored electrodes: 1. To provide additional shielding, people add carbon dioxide gas with the flux. 2. The flux core can provide all of the slagging materials and shielding gas on its own. The carbon dioxide gas shield creates a deeply penetrating arc and usually results in a better weld than an external gas shield. Although flux-cored arc welding works in three ways: semi automatically, automatically, or by machine. The wire feeder continues to feed the electrode wire, and the power source retains the arc length in semiautomatic welding. The welder changes the welding parameters and manipulates the welding gun. Machine welding uses flux-cored arc welding, where the machinery feeds the wire, maintains the arc length, and provides joint travel. For this reason, the welding operator constantly monitors the welding and adjusts the welding parameters. Automatic welding enables high-volume production. Why should you use flux-cored wires? By optimising flux-cored wire, achieving performance is possible. A flux-cored wire can perform better and faster in many welding applications. Flux-cored welding wire suppliers provide materials for flat welding, vertical-up welding, and welding hard-to-weld steels. However, it has limitations and drawbacks. GMAW, for example, is slow for out-of-position welding. It is restricted to short-circuit transfer which is due to the risk of lack-of-fusion or pulse transfer. Hence, it requires a specialised welding power source. It also necessitates spotless steel. The ability to add various objects to the centre of the welding wire enables numerous performance improvements. Slag formers protect the weld pool and shape and support the weld. Iron powder helps in increasing the speed of the deposition process. Similarly, powdered alloys create low-alloy deposits or improve mechanical properties. In deed, scavengers and fluxing agents are useful to refine the weld metals. Flexible shape and size The self-shielding electrode performs precisely what its name suggests. Shielding gas is not needed to protect the hot weld. Flux material is used to make FCAW electrode, which provides sufficient shielding from the atmosphere. As a result, it is an ideal choice for general repairs and one of the best outdoor welding options. Because dual shielding electrodes do not require shielding gas, the process is a more uncomplicated and minimal cost. Shielding gas is required for dual-shielding electrode protection against rust and corrosion. Contact flux-cored welding wire manufacturers in Mumbai to choose the perfect shielding gas. Also, a mixture of 25% carbon dioxide gas and 75% argon gas will suffice in most cases. Therefore, ensure to make the best choice to avoid rework to remove defective and poor quality welds. There are two types of flux-cored wires in today’s market: gas shielded flux cored wires (FCAW-G) and self-shielded flux-cored wires (FCAW-S). Gas shielded flux cored wire: The core ingredients for this category of flux-cored wire is formulated to achieve performance. The shielding gas protects the core materials, so choosing the material becomes vital. Additionally, a perfect material can optimise a specific area of welding performance. It includes achieving smooth spray-type transfer with 100% carbon dioxide shielding gas. Furthermore, the welding speeds double in the vertical position. Self-shielded flux cored wire: Around 1961, self-shielded flux-cored wires (FCAW-S) were introduced to the market after gas-shielded flux-cored wires. What distinguishes them from Gas Shield Flux core wires? Certainly, self-shielded flux-cored cables do not require shielding gases. Indeed the wire’s core materials produce its shielding gases. Additionally, it refines the welding pool. Ideal for outside use The simplicity of self-shielded flux-cored wires is one of its advantages. Furthermore, they should be able to use it outdoors in high winds without the need for tents or additional gas shielding equipment. Are you looking for reliable flux-cored welding wire manufacturers? Get in touch with us!
MIG Welding process – What you should know
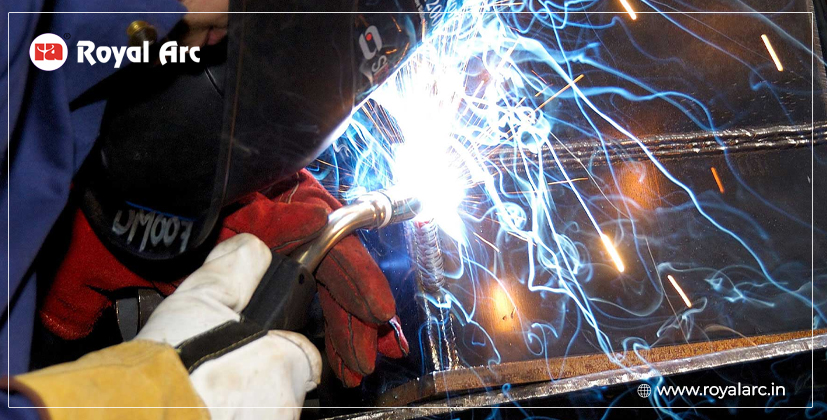
The welding wire wound in a coil is automatically fed into the welding flame by the feeding motor in CO2 arc welding. The electrode is the wire that undergoes energising process when the base metal and electrode strikes in the welding. To link two base metal pieces, the arc heat melts the wire and the base metal. CO2 gas emits from the nozzle of the welding flame to shield the weld pool in this situation so that oxygen and nitrogen in the atmosphere does not affect the weld metal MIG Welding Wire: Flux-Core vs Solid Flux-core and solid MIG welding wire are the two most common types of MIG welding wire. A flux-core wire is a metal electrode with a “flux compound” inside it. When the wire melts and reacts with the welding arc, the formation of the gas occurs. As a result, the gas aids in protecting the weld from oxygen, which can cause problems. This implies that no shielding gas is necessary for this type of wire. However, the usage of the shielding gas in conjunction with flux-core wire gives more protection in some instances. MIG welding wire manufacturers supply Solid wire electrodes for many industries. This necessitates the deployment of shielding gas. 75% argon and 25% carbon dioxide is the most popular shielding gas. For this purpose, co2 wire manufacturers provide one of the finest qualities for welding. To prevent oxidation and flaws in the weld, the welding cannon supply a continuous stream of gas from a container surrounding the electrode and weld region. MIG wire supplier offers a range of materials that serve MIG welding wire types (solid and flux-core). Some common materials include aluminium, stainless steel, copper, and silver. The usage usually depends on the welding objective. There are a few things to keep in mind when it comes to MIG welding wire. Are you unsure what to consider while selecting MIG welding wire? Neither style is superior to the other; instead, the best option is dependent on your circumstances and tastes. When choosing MIG welding wire, keep the following points in mind. Material Solid MIG welding wires used with shielding gases generate a cleaner weld with fewer spatter than flux-cored wire. Spatter does not always influence weld quality. Therefore, it utilises the solid wire in most typical circumstances. Yet, it requires further grinding, polishing, or finishing before painting or other surface preparations. Different types of materials use different types of wire. You can make use of ER70S-3 wire to clean, oil-free, and rust-free mild steel. Yet, co2 mig wire manufacturers in India offer wire that contains a deoxidiser. Later, mild steel affected by corrosion or mill scale uses the deoxidiser for further processing. A flux-core wire is frequently a superior solution in very windy or demanding outdoor conditions. In particular weather, condition wind can blow away the gas used to shield solid MIG welding wire. It results in a lower-quality weld unless you use a windscreen. The insulation of the metal is more efficient in any circumstance. It is due to the heating process of flux-core wire that generates gases. The thickness of wire – We recommend thicker wire for thicker work pieces. It requires multiple passes to generate a robust weld. The standard for most welds is 035-inch diameter wire, although this may not be enough for excessively thick metal parts. Weld unit power is inversely proportional to wire thickness. The higher a MIG welding unit’s voltage and power, the greater the thickness it can accommodate. With lower-powered MIG welding equipment, thicker wire is not a good idea. Because of the decreased overall amperage and output, the work pieces may fail to melt correctly and make a quality weld. Always ensure to check the manufacturer’s instructions for the maximum wire thickness. Tips for proper maintenance When it comes to MIG welding, avoiding typical blunders can help you achieve the most satisfactory outcomes. Maintaining the MIG gun and consumables, such as the contact tip, nozzle, and liner is equally vital. Check that the gas holes in the nozzle are clean and that the seat that holds the contact tip isn’t packed with splatter or debris whenever you change consumables. Overheating in the gun and handle might be caused by a blocked contact tip or nozzle. Ensure all connections are tight and as concentric as feasible regularly. A MIG gun is more effective and efficient if the gun and cable are kept as straight as possible during welding and then laid flat to cool. You should always purchase high-quality MIG welding wire, regardless of the type of MIG welding wire you are buying. Quality MIG wire is more forgiving than lower-quality welding wire, can produce a more sound weld even in less-than-ideal conditions, and costs a fraction of the total welding cost. Do you require assistance in selecting the appropriate products? Please contact mig welding wire manufacturers in India with further details about your job and circumstances, and one of our professionals will be pleased to assist you.